Prolongación de la vida útil: cómo su equipo de petróleo y gas puede beneficiarse del revestimiento con cepillo
En la industria del petróleo y el gas, los equipos funcionan en entornos hostiles. Se espera que los componentes resistan el desgaste, la corrosión, las fluctuaciones de temperatura y presión, y los operadores necesitan soluciones de reparación que se puedan completar en el menor tiempo posible, produciendo resultados sobresalientes que pueden mantener los componentes protegidos contra daños mayores.
SIFCO ASC perfeccionó un proceso que puede reparar componentes grandes, como componentes de ensamblaje de BOP, cuerpos de colgadores de tubería, mandriles internos, cilindros, carcasas, juntas ascendentes y más. Algunas sin necesidad de desmontar.
El SIFCO Process® de metalizado selectivo es único. Es un método portátil de galvanoplastia en áreas localizadas sin el uso de un tanque de inmersión. El depósito se aplica en áreas desgastadas o dañadas para redimensionar, reparar o mejorar el rendimiento del componente. Los depósitos extremadamente adherentes se aplican de manera uniforme y precisa, eliminando en algunos casos la necesidad de un mecanizado posterior. Además, la mano de obra experimentada y calificada de SIFCO ASC cuenta con certificaciones para trabajar en plataformas petroleras, lo que permite un despliegue rápido cuando sea necesario.
El SIFCO Process® es muy apreciado en la industria del petróleo y el gas y se utiliza en muchas aplicaciones OEM y de reparación. Si bien todos los depósitos se aplican siguiendo estrictamente cualquier especificación o requisito de calidad, el proceso ya cumple con las especificaciones de FMC, GE Oil & Gas, Halliburton, Schlumberger, Tenaris-Hydril, Vallourec y VAM.
SIFCO ASC está equipado para respaldar a la industria y reducir la amenaza de la corrosión mientras cumple con los desafíos clave de extender la vida útil del equipo, reducir el tiempo de inactividad y reducir los costos operativos.
Para extender la vida útil de su equipo, o si desea obtener más información sobre nuestros servicios de petróleo y gas, visite nuestra página web. Contáctenos hoy al 800-765-4131 o info@sifcoasc.com
Ingeniería del trineo de Santa Claus
El siguiente es un blog invitado de Surface Technology
En cuestión de días, Papá Noel partirá del Polo Norte en su famoso trineo rojo. Cargado con los juguetes imprescindibles de este año, Hatchimals y Star Wars, viajará 317 millones de millas a través de océanos y continentes durante toda la noche de Nochebuena.
Alimentados con una mezcla de galletas, cacao caliente y zanahorias, Papá Noel y sus renos tienen una enorme tarea para asegurarse de que los millones de niños de todo el mundo reciban sus regalos por Navidad.
Hemos pensado en intentar comprender la ingeniería de superficie necesaria para que Papá Noel y sus renos cumplan su épica misión anual.
Desgraciadamente, no disponemos de ninguna información de la muy secreta Elf R&D -sin duda el centro de investigación y desarrollo más eminente del mundo-, pero utilizando nuestro propio equipo técnico, hemos considerado los requisitos únicos del trineo de Santa Claus y hemos esbozado la mezcla de revestimientos que bien podría utilizarse.
El trineo
Con sólo 32 horas para completar todas sus entregas, la velocidad es esencial para Papá Noel. Hay muchas teorías sobre cómo el trineo se propulsa a un 0,97% de la velocidad de la luz: desde que los renos comparten el mismo nutricionista que el equipo olímpico ruso de 2012, hasta la propulsión por cohetes.
Sin embargo, lo que sí sabemos es que será importante un revestimiento capaz de funcionar eficazmente a altas temperaturas. Los revestimientos cerámicos, como los utilizados por la NASA en sus transbordadores espaciales, son una opción viable para los paneles de la carrocería del trineo.
Proyección térmica, como HVOF también puede utilizarse para cualquier componente móvil, como los componentes de la turbina (si se utiliza la propulsión de cohetes), debido a su capacidad para funcionar a altas temperaturas y proporcionar una mejor protección contra el desgaste, la corrosión, la fatiga y la oxidación a altas temperaturas; lo último que necesita Santa es un mal funcionamiento mecánico con un calendario tan apretado.
Corredores de trineo
Con tantas entregas que hacer, los corredores al pie del trineo de Papá Noel harán millones de aterrizajes y despegues. Un juguete roto no sirve para la mañana de Navidad, así que un aterrizaje suave es esencial.
Creemos que el chapado selectivo puede utilizarse en el taller de los elfos cada año para asegurarse de que los corredores de Santa Claus se mantienen y están listos para el despegue navideño. Utilizando el Proceso SIFCO® se podría utilizar níquel o cadmio para volver a revestir las zonas desgastadas o astilladas de los patines. Además, el proceso está aprobado por la FAA, lo que mantiene a Papá Noel fuera de la lista de los malos de la Autoridad Federal de Aviación.
Frenos
Suponemos que los renos se encargan de detener el trineo en cada punto de bajada, pero para obtener un poco más de potencia de frenado los elfos de Papá Noel pueden haber optado por un sistema de frenado mecánico. Para que Papá Noel no se pierda ni una sola parada, se podría utilizar una combinación de chapado de aleación de zinc y revestimiento de polvo (RAL 3020, por supuesto), o incluso un revestimiento de cerámica.
Climatización
Al atravesar los cielos de todos los lugares, desde Afganistán hasta Zimbabue -y 194 países entre ellos-, Santa Claus estará expuesto a temperaturas que van desde los cero hasta los 95 grados.
Suponemos que el traje de Papá Noel está fabricado con los mejores materiales de Laponia, pensando tanto en el calor como en la transpirabilidad, pero para mayor comodidad, sobre todo en climas cálidos, los elfos pueden haber equipado el trineo de Papá Noel con aire acondicionado.
Mientras que Surface Technology, SIFCO ASC y Ultraseal proporcionan servicios para muchos proyectos interesantes de ingeniería y fabricación, la respuesta a cómo Papá Noel y sus renos entregan todos esos regalos en Nochebuena tendrá que seguir siendo un misterio durante otro año.
Deseamos a todos nuestros clientes de todo el mundo una muy feliz Navidad y un próspero Año Nuevo.
Descubra la eficiencia en las reparaciones aeroespaciales con un seminario web
En SIFCO ASC, sabemos que conseguir mayores niveles de eficiencia es quizás uno de los mayores retos a los que se enfrentan muchos de nuestros clientes. Para la industria aeroespacial, que está experimentando un aumento de la demanda en el sector comercial, la eficiencia es aún más importante. Si combinamos este reto con los requisitos legislativos que regulan el uso de productos químicos como el cadmio, los profesionales del sector se enfrentan a un panorama operativo difícil.
Seminario web gratuito: Revestimiento Selectivo y anodizado para el sector aeroespacial
Por ello, SIFCO ASC organiza un seminario web gratuito. Impartido por Danijela Milosevic-Popovich – Directora de Investigación y Desarrollo de SIFCO ASC – Spec’d In: Brush Plating & Anodizing for Aerospace proporcionará información y consejos de expertos para los fabricantes de la industria aeroespacial.
Diseñado para ofrecer información sobre cómo superar los retos a los que se enfrentan los fabricantes y operadores hoy en día, el seminario web ayudará a los asistentes a comprender los procesos de chapado selectivo y anodizado y cómo mejoran las opciones de reparación eficiente de los componentes aeroespaciales.
Las ventajas del revestimiento selectivo frente al revestimiento de tanques
dijo Danijela: “Nuestro seminario web está diseñado para ofrecer a los asistentes una visión experta sobre el uso de la galvanoplastia selectiva y el anodizado, y cómo estos procesos están ayudando a impulsar una mayor eficiencia dentro de la cadena de suministro aeroespacial. Los procesos ya están especificados en los manuales de revisión y de prácticas estándar, por lo que este seminario web analizará cuándo y por qué deben utilizarse estos procesos en lugar de otras alternativas como el chapado de tanques. También compartiremos ejemplos reales que demuestran el ahorro de tiempo y costes asociado a los procesos, así como el modo en que los clientes pueden utilizar la automatización para mejorar la calidad y la consistencia de sus operaciones de metalizado.
Impulsar la eficiencia en el sector aeroespacial
“El sector aeroespacial se encuentra en un momento emocionante y desafiante a la vez. El sector es extremadamente boyante con una demanda creciente, sin embargo, esto pone una tensión en los fabricantes a lo largo de la cadena de suministro, mientras que el mercado de MRO está bajo una mayor presión para mantener las aeronaves en funcionamiento durante el mayor tiempo posible. Nuestro seminario web ayudará a los fabricantes a entender cómo pueden maximizar la eficiencia, haciéndolos más competitivos y elevando los niveles de calidad en toda la industria.”
Buscar la reparación correcta de los defectos
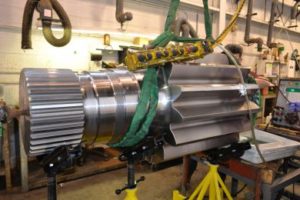
En la industria minera, las piezas y componentes de repuesto para los equipos industriales no suelen estar a mano, o no son fáciles de conseguir debido a su tamaño, coste y plazo de entrega. Por ello, los operadores necesitan un proceso oportuno para reparar sus componentes en la propia empresa o arriesgarse a incurrir en costes adicionales debido a las horas perdidas y al tiempo de inactividad prolongado.
Este fue el caso de un fabricante de engranajes con sede en Cleveland, Ohio, cuando fue necesario reparar el engranaje de piñón de una excavadora de arrastre. El engranaje del piñón forma parte de un conjunto de tren de engranajes, y si no se mantienen con regularidad, el lubricante puede filtrarse por la junta y hacer que el rodamiento se agarre y se agriete al eje. Cuando esto ocurrió, se encargó a Horsburgh & Scott Co. la tarea de volver a poner en funcionamiento el equipo y, en última instancia, la grúa.
Cuando se retiró el rodamiento agarrotado, también se eliminó el exceso de material del gorrón, lo que dio lugar a una gubia en el acabado de la superficie.
Las técnicas de reparación tradicionales, como la soldadura, el enfundado y la pulverización de metal, pueden llevar de cuatro a seis semanas debido al tiempo de desmontaje y envío, lo que supone un tiempo de inactividad prolongado, además de ser costoso.
El rodamiento en cuestión había incurrido en una gubia que medía 0,030″ de profundidad, 0,75″ de ancho y 12″ de largo, lo que lo convertía en 0,012″ de tamaño inferior. Cuando se utiliza el revestimiento selectivo, los defectos se reparan normalmente con una o más capas de cobre, y luego se cubren con un depósito resistente al desgaste que tiene buenas características de liberación o humectación. En este caso, el gorrón del cojinete se chapó primero con un espesor de 0,001″ de cobre y luego se enmascaró para la reparación del defecto. El ánodo que se utilizó para rellenar el defecto, cubrió toda la longitud de la gubia que se rellenó con tres capas de cobre y se terminó a mano entre ellas. La capa final se alisó y luego se chapó con un espesor de 0,006″ de níquel utilizando un chapador ID.
Al utilizar el SIFCO Process®, Horsburgh and Scott Co. no sólo pudo devolver la grúa al servicio con un tiempo de inactividad mínimo, sino que también pudo mejorar el tiempo entre fallos y ahorrar costes significativos en comparación con los métodos de reparación alternativos.
El SIFCO Process® puede utilizarse en otras áreas de la industria minera, incluyendo:
VEHÍCULOS TODOTERRENO (OHV)
- Casos
- Bujes de rueda
- Carcasas de los diferenciales
EQUIPO DE PERFORACIÓN
- Carcasas de las secciones
- Carcasas de bombas hidráulicas
Si desea más información sobre el Proceso SIFCO®, póngase en contacto con info@sifcoasc.com o llámenos al 800-765-4131.
El CRAIC está listo para despegar
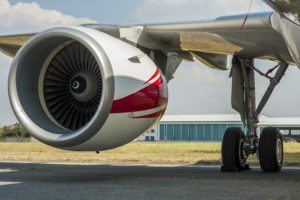
El mes pasado, China y Rusia se asociaron para lanzar la Corporación Internacional de Aviones Comerciales China-Rusia (CRAIC). Su objetivo, construir un avión de 280 pasajeros de doble pasillo y fuselaje ancho para competir con Airbus y Boeing, tendrá un coste estimado de entre 13.000 y 20.000 millones de dólares. Según Aviation Week, el CRAIC aspira a lanzar su primer vuelo en 2022 o 2023 y a estar plenamente operativo en 2025-2027.
Mientras que la sede y el ensamblaje de CRAIC estarán en Shangai, la investigación y el desarrollo del avión estarán en Moscú (Rusia). El grupo, aún en sus inicios, está buscando proveedores de motores. Al igual que los demás reactores modernos, el avión chino-ruso de 280 plazas, o C929 (su denominación no confirmada), se integrará con toda probabilidad en la cadena de suministro mundial y utilizará fabricantes de motores como Pratt & Whitney, GE y Rolls-Royce; así como otros fabricantes occidentales como Honeywell y United Technologies para la aviónica de su cabina y los sistemas de vuelo.
Esto es una buena noticia para la industria del acabado de superficies y posiblemente para el medio ambiente. Al desarrollar un nuevo avión, CRAIC no está obligado a utilizar los sistemas y planos heredados que utilizan revestimientos de cadmio para la protección contra la corrosión. En su lugar, se pueden utilizar nuevas alternativas de calidad y respetuosas con el medio ambiente, como el zinc-níquel o el estaño-zinc. Al incorporar los nuevos materiales a las especificaciones de los fabricantes de equipos originales, las últimas aplicaciones de retoque en los trenes de aterrizaje, las pistas de los flaps, los orificios de los casquillos y otros componentes estructurales, también pueden utilizarlos, ayudando esencialmente a eliminar el cadmio.
El CRAIC cree que una de las principales ventajas de romper el duopolio de Airbus y Boeing será la reducción de costes. Esperan que, al diseñar un avión con menores costes de explotación, se interesen más compradores internacionales. También tienen previsto vender servicios de mantenimiento, servicios logísticos y paquetes de actualización para obtener ingresos adicionales.
Para obtener información sobre las alternativas al cadmio, visite nuestro Centro de conocimientos sobre el cadmio.
Para leer el artículo completo de Jeffrey Lin y P.W. Singer para Popular Science, visite www.popsci.com
Reparación de componentes para las máquinas más duras de la Tierra
Mejorar la vida útil de los componentes vitales es un factor importante para cualquier fabricante, especialmente para aquellos que diseñan y producen vehículos de misión crítica para entornos altamente corrosivos, como la industria minera.
Cuando se trata de una operación minera pesada, la producción ininterrumpida, las implacables condiciones operativas y el tamaño y el peso del equipo causarán daños y un considerable desgaste en los componentes comunes. Algunos componentes plantean problemas de mantenimiento debido a su tamaño y ubicación prohibitivos, como los sistemas hidráulico y de transmisión; y los componentes de la transmisión final.
Aunque los fabricantes desean encontrar una solución para evitar la necesidad de desechar piezas, también quieren maximizar el rendimiento de los componentes, reducir el tiempo de inactividad y ejecutar una reparación probada antes del fallo.
Las ventajas del revestimiento selectivo con cepillos incluyen la capacidad de enfocar con precisión el revestimiento en áreas específicas de un componente, permitiendo que las piezas se revistan in situ, lo que puede reducir drásticamente el tiempo de inactividad y minimizar los retrasos en la producción. El chapado selectivo es el más adecuado para zonas localizadas en diámetros interiores y exteriores o superficies planas. A diferencia del revestimiento de tanques, el revestimiento con cepillos selectivos no requiere un extenso enmascaramiento ni accesorios especiales para revestir el componente.
La duración de una operación de revestimiento viene determinada principalmente por la cantidad de material que hay que aplicar. En los sistemas de revestimiento selectivo con cepillos, líderes en el mercado, los depósitos pueden ser revestidos a velocidades entre 30 y 60 veces más rápidas que el revestimiento convencional con tanques. Las diferencias de rendimiento y coste que estos factores pueden suponer para el mantenimiento, la mejora o la reparación de componentes críticos pueden ser significativas.
Aunque los daños causados por el desgaste, la corrosión o el mecanizado incorrecto pueden repararse mediante el revestimiento con cepillos selectivos, esta solución innovadora no debe considerarse únicamente para la reparación o el salvamento. Toda la gama de depósitos de metales puros y aleaciones disponibles ofrecen una mayor resistencia al desgaste, una mayor dureza superficial, una baja resistencia al contacto eléctrico o una protección contra la corrosión; todas ellas consideraciones importantes para la industria minera.
Para obtener más información sobre la innovadora tecnología y soluciones de revestimiento con cepillos selectivos de SIFCO ASC, profundice aquí: www.sifcoasc.com/mining.
Celebre el Ascenso Directo en el Día Mundial del Helicóptero
El Día Mundial del Helicóptero es el domingo 19 de agosto de 2018.
El Día Mundial del Helicóptero tiene como objetivo concienciar sobre las contribuciones sociales que hacen los helicópteros. Al reconocer estas increíbles máquinas, también estamos reconociendo a la industria que las apoya desde el diseño, hasta los pilotos y el apoyo.
Cuando se piensa en helicópteros, pueden venir a la mente las misiones de rescate, los transportes médicos, las labores de ayuda en caso de catástrofe y la cobertura mediática. Pero su uso va mucho más allá. Se calcula que hay más de 55.000 helicópteros en todo el mundo, de los cuales casi el 40% son de propiedad militar. Los helicópteros son codiciados por su huella de despegue y aterrizaje y su capacidad para acceder a zonas de difícil acceso a las que ni un vehículo ni un avión pueden acceder.
SIFCO ASC lleva apoyando al sector de los helicópteros desde mediados de la década de 1970. Durante más de 40 años, los principales fabricantes han confiado en el Proceso SIFCO® para el revestimiento selectivo de componentes, desde conjuntos de rotores de cola y de elevación, conjuntos de tubos, ejes, orificios y otros.
Resultados probados
El pilón de la sección de cola de un helicóptero Sikorsky SH-60B Seahawk experimenta un importante desgaste en las orejetas de soporte. Debido a la función del pilón -que gira y se bloquea para su almacenamiento o se retira para el mantenimiento del AOG-, las lengüetas de soporte requieren que se retoque el chapado de cadmio cuando se retiran los pasadores de bloqueo. Al utilizar el SIFCO Process®, la operación de chapado se lleva a cabo in situ y sólo se tarda 5 minutos por lengüeta, lo que ahorra horas de tiempo de inactividad.
En el caso de Lord Corp., el anodizado del tanque provocó una pérdida de dimensión en el diámetro interior de la bisagra de retraso del conjunto del rotor del helicóptero Bell 407. Si bien el mecanizado de los orificios restauró la dimensión, también eliminó el revestimiento anódico. Se eligió el anodizado selectivo para proteger la corrosión y mejorar los plazos de entrega. En un día se completaron 24 piezas, en comparación con los casi cuatro días que se tarda en procesar el anodizado en tanque.
Para saber más sobre el apoyo de SIFCO ASC a la industria aeroespacial, visite nuestra página web sobre la industria aeroespacial. Para saber más sobre el vuelo del primer helicóptero del mundo, lea nuestro blog: “Esta semana en la historia: el primer helicóptero práctico de Estados Unidos”.
“El equipo de SIFCO ASC ha entendido siempre nuestros requisitos específicos para varios proyectos de mantenimiento y reparación aeroespacial. El servicio de atención al cliente del equipo es ejemplar, con buenos tiempos de respuesta en las consultas y plazos de entrega flexibles en las reparaciones. SIFCO ASC es un socio de confianza de Heliwork Services y proporciona la calidad y el servicio que necesitamos”.
El cadmio y la necesidad de alternativas en la aviación
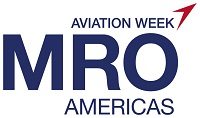
Mientras deshacemos el equipaje de MRO Americas, revisamos nuestros folletos, tarjetas de visita y chucherías, lo que nos permite reflexionar sobre la información que hemos recopilado y los contactos que hemos conocido. Aquí, en SIFCO, el tema que resonó, y que nuestro equipo notó, fue el de los sustitutos del cadmio y la necesidad de alternativas de mantenimiento respetuosas con el medio ambiente en la industria aeroespacial.
Se sabe que la exigente industria aeroespacial requiere soluciones bien diseñadas, pero muchos temen desviarse de las aplicaciones ya establecidas, aunque puedan suponer un riesgo para el operador y el medio ambiente. Y aunque existan soluciones probadas.
Reconocemos que el chapado selectivo, y el acabado de superficies, son aplicaciones de mantenimiento esenciales en MRO. Por ello, SIFCO ha desarrollado y perfeccionado sus productos a lo largo de los últimos cincuenta años para ofrecer los depósitos adherentes de mayor calidad que se necesitan para satisfacer los requisitos siempre cambiantes de la industria.
El cadmio es un depósito muy conocido y utilizado para aplicaciones de protección contra la corrosión en el tren de aterrizaje, los casquillos, las pistas de los flaps y otros componentes estructurales del avión. Pero el cadmio también es un conocido carcinógeno. Y el riesgo que supone para el operador y el medio ambiente es la razón por la que SIFCO desarrolló sus alternativas al cadmio hace más de 15 años.
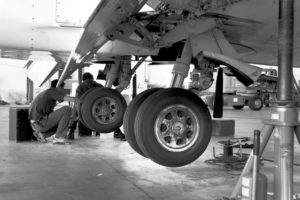
Las alternativas al cadmio de SIFCO son depósitos de calidad superior que son sustitutos directos en el proceso de revestimiento con cadmio. El LHE de zinc-níquel y el LHE de estaño-zinc son alternativas menos tóxicas al cadmio que pueden utilizarse para reparar cadmio dañado, zinc-níquel, estaño-zinc y aluminio DIV dañado en aceros de alta resistencia. Ambos depósitos proporcionan una excelente protección contra la corrosión y son de baja fragilidad por hidrógeno, y no requieren un horneado de alivio de la fragilidad por hidrógeno posterior al revestimiento. Cuando se utiliza junto con la Conversión de Cromo Trivalente de SIFCO, puede lograr 1.000 horas de niebla salina sin corrosión del metal base. Estos depósitos de zinc-níquel y estaño-zinc son capaces de cumplir los requisitos de rendimiento de AMS 2451/9, AMS 2451/10 y BAC 5664.
Para obtener más información sobre las alternativas al cadmio de SIFCO, haga clic aquí o póngase en contacto con nosotros en info@sifcoasc.com.
Conexiones de autobús: Por qué tienen sentido los depósitos plateados localizados
En la industria eléctrica, la optimización del flujo de energía es una preocupación primordial para los procesos de generación, transmisión y distribución. La clave es proporcionar y mantener uniones conductoras de baja resistencia mediante depósitos plateados.
La experiencia de campo y los estudios de laboratorio han demostrado que esto es especialmente cierto en el caso de las barras colectoras y las conexiones atornilladas de alta corriente. En concreto, las barras colectoras plateadas superan a las no plateadas al ofrecer una resistencia de contacto estable y una baja temperatura máxima de funcionamiento que aumentan la vida útil de la unión del bus. Y lo que es más importante, las juntas de resistencia de contacto estables reducirán la necesidad de un mantenimiento frecuente, disminuirán el tiempo de inactividad general de los equipos y reducirán en gran medida el riesgo de fallos catastróficos.
Las buenas prácticas de la industria recomiendan que todos los contactos del bus sean plateados. La mayoría de las especificaciones gubernamentales, de la IEEE y de los proveedores de seguros exigen que todas las conexiones de bus atornilladas estén chapadas de acuerdo con las especificaciones aplicables.
Uno de los elementos clave para un chapado eficaz de los contactos de las barras colectoras es la aplicación de un depósito uniforme de grosor suficiente para proporcionar protección contra la corrosión y un “efecto de nivelación” para aumentar la superficie de la unión del bus.
El chapado con cepillos, utilizando plata pura, proporciona una solución sencilla y rentable para el chapado in situ de los sistemas de bus durante el mantenimiento rutinario y también puede ser útil para mejorar el bus, en lugar de sustituirlo, cuando se desea aumentar la capacidad del generador o del sistema.
Los primeros años
En las centrales eléctricas más antiguas, se instalaban las barras colectoras de aluminio o cobre. Mientras que el rendimiento de una junta de bus sin recubrimiento podía ser suficiente hace años, las crecientes demandas de energía de hoy en día, dada la capacidad limitada y las economías de mercado, están obligando a los productores a mejorar la eficiencia y el rendimiento de todo el sistema.
Muchas de las primeras conexiones de los autobuses no se han soltado desde que se instalaron por primera vez en 1910. Las conexiones de autobús tienen varios factores que limitan su rendimiento durante la vida útil, entre ellos:
- Irregularidades en las superficies de contacto
- Contaminación por partículas antes de la instalación
- Oxidación
Estos factores, cuando se combinan, tienen un efecto de aumento de la resistencia de contacto y de la temperatura y, por lo tanto, disminuyen la eficacia de la junta con el paso del tiempo, pudiendo causar fallos catastróficos. Incluso cuando es nueva, las imperfecciones de la superficie de cobre de la barra colectora hacen que sólo una fracción de esa superficie entre en contacto directo con su conexión. Según algunas estimaciones, esa fracción puede ser tan baja como el diez por ciento. Aunque el aumento de la fuerza de contacto puede aplanar las zonas altas, los efectos son mínimos y pueden incluso suponer una tensión no deseada en el sistema de fijación.
La formación de películas superficiales no conductoras debido a los contaminantes atmosféricos nocivos es también un factor que limita la fiabilidad de las juntas, incluso en los contactos atornillados. La fritura reducirá la resistencia de contacto de las películas de superficie fina, pero las películas más gruesas y tenaces pueden seguir presentando un problema que se verá magnificado por el aumento de la temperatura en la unión debido a la mayor resistencia. La fritura es la aparición de la ruptura dieléctrica de una película de contacto. Un gradiente de potencial de 100V/μm podría ser suficiente para provocar esta ruptura dieléctrica.
La oxidación del material de los autobuses es un hecho constante, a menos que se tomen medidas para evitarla con un revestimiento de barrera. La formación de capas de oxidación en el material del bus dentro de los empalmes provoca un aumento de la resistencia y, por lo tanto, un aumento de las caídas de tensión y de las temperaturas locales. Se ha informado de que la resistencia de la unión a través del bus sin recubrimiento puede aumentar más del 20% debido a la formación de oxidación. Los estudios han demostrado que el revestimiento de plata de las juntas del bus reduce significativamente la oxidación del material del bus en servicio.
Los efectos combinados de las superficies irregulares, la contaminación y la formación de películas superficiales no conductoras y la oxidación pueden crear “puntos calientes” que deteriorarán aún más la fiabilidad y el rendimiento de la junta.
Una articulación mejor
Las pruebas y la experiencia sobre el terreno han demostrado que se puede adoptar una medida sencilla para minimizar los efectos de las superficies de contacto irregulares y la formación de óxidos y otras películas superficiales en el rendimiento de las juntas. Este paso consiste en revestir la zona de unión con un material suave, conductor y resistente a la corrosión. La aplicación de un depósito de 0,0002″ a 0,0005″ de grosor, como plata, níquel o estaño, puede mejorar el rendimiento de la vida útil de la junta hasta en un 30% y reducir sustancialmente el mantenimiento.
El recubrimiento con un material blando, como la plata o el estaño, forma eficazmente una junta de compresión en las superficies a conectar. La fuerza aplicada al atornillar las superficies aprieta el material conductor en las zonas bajas, lo que aumenta eficazmente el área de contacto y disminuye la resistencia general de la unión.
Las pruebas han demostrado que estos materiales ralentizan en gran medida la formación de óxido de cobre y otras películas superficiales, maximizando la conductividad y minimizando el calor. Una junta plateada permite el funcionamiento a una temperatura más alta sin que la junta se degrade a lo largo de su vida útil. El resultado final, con el tiempo, es un aumento significativo del rendimiento, la eficiencia, la economía y la reducción del mantenimiento.
Debido a la suavidad de la plata, puede adaptarse con mayor precisión a los contornos y hendiduras de la pieza original, aumentando las áreas de contacto reales. La plata proporciona una buena conexión eléctrica evitando la formación de óxido de cobre en las caras de contacto. El recubrimiento de níquel ha mostrado algunas ventajas en cuanto a costes, pero la plata muestra un mayor rendimiento y eficiencia de funcionamiento, mostrando menos resistencia y manteniendo temperaturas más bajas mientras está en servicio.
El chapado de la conexión mediante un baño de plata con cianuro resuelve el problema de proporcionar un espesor suficiente, pero es costoso y requiere mucho tiempo. En el caso de las barras colectoras, deben retirarse completamente del sistema y enviarse fuera para su chapado. Por lo tanto, el mayor tiempo de interrupción que requiere este método puede resultar poco atractivo.
La galvanoplastia, realizada mediante el Proceso SIFCO®, puede completarse in situ con un mínimo desmontaje, durante cualquier parada planificada sin necesidad de retirar el equipo de su ubicación. Para garantizar la seguridad de los operarios y de las personas de los alrededores, SIFCO ASC utiliza plata sin cianuro en su proceso de chapado. Este proceso de revestimiento portátil aplica con precisión la plata sin cianuro a una velocidad de 0,020″ por hora, produciendo un acabado suave y uniforme. Las dos caras de una junta de cobre de 4″ x 4″ pueden enmascararse fácilmente y revestirse con 0,0003″ de plata en menos de 15 minutos.
El grosor deseado para cada aplicación y/o pieza en particular se calcula antes del revestimiento. SIFCO ASC utiliza medidores digitales de amperios-hora para controlar con precisión el grosor del chapado y garantizar unos acabados suaves y un chapado uniforme.
Un acabado liso y un depósito uniforme de suficiente grosor mejorarán significativamente la fiabilidad y el rendimiento de la unión eléctrica.
Mejora del sistema de conductos de autobuses en la presa de Fontana de la TVA
Como parte del amplio programa de modernización de la red hidroeléctrica de la TVA, los sistemas de conductos eléctricos se sustituyen a veces por sistemas nuevos suficientemente dimensionados para las nuevas capacidades de salida de las unidades. Esto ocurre cuando la potencia nominal de una unidad generadora se incrementa más allá de las capacidades de su correspondiente sistema de conductos de bus o cuando la disposición física de la planta debe cambiar para acomodar otros equipos nuevos. Sin embargo, TVA ha demostrado con éxito que muchos sistemas de bus más antiguos pueden ser recalificados a ampacidades más altas mediante el uso de revestimiento de escobillas en el lugar para aumentar la capacidad de transporte de corriente del bus. El éxito depende en gran medida de las uniones atornilladas modificadas porque deben ser estables, fiables y funcionar con una resistencia de contacto reducida para un rango de funcionamiento más amplio. Todo esto puede lograrse con un coste mucho menor que la sustitución de los autobuses.
TVA ha conseguido un ahorro sustancial al optar por chapar las conexiones desnudas existentes en lugar de actualizarlas a un nuevo sistema de bus. Las conexiones atornilladas se platearon in situ durante las paradas programadas.
Pasos de la operación:
- Limpie mecánicamente las superficies de contacto para eliminar los óxidos pesados.
- Limpie con disolvente el contacto y la superficie adyacente para eliminar cualquier rastro de aceite u otros residuos.
- Máscara para definir la zona a chapar.
- Preparación electroquímica
- Placa de la pieza
- Retire el enmascaramiento
Conclusión
El rendimiento de las juntas de contacto depende del mantenimiento de una baja resistencia. La conductividad de la junta se deteriorará naturalmente con el tiempo debido a los rigores del servicio, así como a fuerzas naturales como la oxidación y la humedad.
Las pruebas han demostrado que el revestimiento de las juntas de los buses con un espesor de plata de 0,0003″ a 0,0005″ mejora considerablemente su vida útil. El chapado selectivo in situ con plata sin cianuro puede ser el enfoque más económico, ya que elimina la necesidad de desmontar los componentes y transportarlos a una instalación de chapado externa, a la vez que proporciona rápidamente un depósito de calidad superior y espesor uniforme que resistirá la prueba del tiempo.
Para más información sobre sus conexiones de autobús plateadas, póngase en contacto con nosotros en el 800-765-4131 o en info@sifcoasc.com.
Revestimiento Selectivo en la industria naval
El cepillado es un proceso fuera del tanque que se utiliza para aplicar depósitos galvánicos en zonas localizadas de componentes de a bordo desgastados o dañados para redimensionar y reparar, o para mejorar el rendimiento de esas zonas. Este proceso de revestimiento portátil ofrece una alternativa única a los métodos de reparación, como la pulverización con llama y la soldadura, cuando se requieren espesores de depósito que van desde unas pocas décimas de milésima de pulgada hasta treinta milésimas de pulgada.
El proceso de chapado con cepillo portátil puede utilizarse en cualquier lugar del taller o a bordo del barco. A diferencia de la pulverización con llama y la soldadura, el revestimiento con cepillo se realiza a temperatura ambiente y no conlleva ningún riesgo de deformación del componente que se está reparando. Los depósitos extremadamente adherentes se aplican de manera uniforme y precisa, eliminando en muchos casos la necesidad de operaciones de mecanizado.
Las aplicaciones típicas incluyen la reparación de condiciones fuera de tolerancia en la carcasa de los engranajes de reducción y en las zonas de los cojinetes de los ejes; la reparación in situ de daños en los cilindros hidráulicos; el redimensionamiento de los ejes y las carcasas de los cojinetes de las bombas y los motores/generadores; la reparación de cortes de vapor en las caras de acoplamiento de las carcasas de las turbinas; y la reparación in situ de los asientos de los cojinetes del cigüeñal desgastados en los motores diésel.
La industria naval lleva más de cuarenta años utilizando el cepillado en aplicaciones muy exigentes. Está aprobado por el American Bureau of Shipping, Lloyds of London y la US Navy. Este proceso flexible proporciona una alternativa viable y rentable a la pulverización con llama y a la soldadura cuando se necesitan espesores de metal más bajos para la reparación de componentes de a bordo.
Para obtener más información sobre cómo se utiliza el revestimiento selectivo en la industria naval, haga clic aquí.