SIFCO ASC aumenta la producción y reduce el plazo de entrega de Polamer con un proceso de metalizado selectivo propio
Como empresa de fabricación aeroespacial global especializada en componentes aeroespaciales complejos para aplicaciones exigentes, Polamer Precision tiene un fuerte enfoque en la calidad.
Después de trabajar con SIFCO ASC en una aplicación de revestimiento para un componente del motor durante muchos años, la empresa aprovechó la experiencia de los ingenieros de SIFCO ASC para llevar el proceso a la empresa. Este cambio ayuda a Polamer a aumentar el rendimiento, ahorrar costes y garantizar la propiedad total del proceso de gestión de la calidad.
Metalizado selectivo en la industria aeroespacial
Los componentes aeroespaciales tienen que ser capaces de soportar la fricción, las altas temperaturas y los entornos corrosivos sin dejar de funcionar a niveles óptimos. El rendimiento y la fiabilidad de los componentes son primordiales, mientras que las estrictas normativas y la competencia del mercado obligan a los fabricantes a encontrar soluciones innovadoras para cumplir los requisitos.
La galvanoplastia selectiva ofrece un método de galvanoplastia de áreas localizadas sin el uso de un tanque de inmersión. En comparación con los métodos tradicionales de revestimiento de tanques, el proceso utiliza un menor volumen de productos químicos, lo que ofrece un menor impacto medioambiental a un menor coste. Los depósitos tienen una excelente adherencia y pueden ser revestidos a velocidades entre 30 y 60 veces más rápidas que el revestimiento convencional de tanques.
Estación de trabajo de revestimiento personalizada
Thomas Chapman, Director de Ventas del Noreste de SIFCO ASC, dijo: “El proceso fue realizado anteriormente por uno de nuestros talleres, que se encargó del proceso de chapado de principio a fin.
“Con el fin de aumentar el rendimiento, acortar los plazos de entrega y satisfacer el aumento de la demanda, trabajamos con el equipo de Polamer Precision para especificar e instalar una estación de trabajo a medida, permitiéndoles incorporar el proceso en su propia línea de producción.”
La estación de trabajo en sí está construida con polipropileno resistente a los productos químicos y está diseñada pensando en la comodidad y la facilidad de uso del operario. La superficie de trabajo está diseñada para alojar equipos auxiliares, incluido el sistema de flujo AeroNikl® que se utiliza para esta aplicación concreta.
La instalación interna también cuenta con utillaje y accesorios de montaje, incluido un software de control programable para el paquete de energía que ha sido diseñado para identificar y reducir la variación de causas especiales y reducir el retrabajo.
Software de control programable y seguimiento del control de procesos
El software de control programable permite a Polamer supervisar y controlar el proceso de dos maneras. En primer lugar, les da la posibilidad de controlar pasivamente el proceso ajustando manualmente los voltios, los amperios y los amperios hora. Para un control más estricto del proceso, el software también facilita la programación activa de todos los pasos, lo que mitiga la posibilidad de que el operario cometa errores.
En los procesos de control de baños, los tipos de software de seguimiento de procesos similares suelen limitarse a la supervisión por lotes de piezas. Lo que es único en el seguimiento del control del proceso de SIFCO ASC es que, a diferencia del revestimiento por baño, supervisa los parámetros de revestimiento por superficie de revestimiento.
De este modo, Polamer no sólo puede recopilar datos de control del proceso pieza por pieza, sino que además puede recopilar información específica sobre las superficies de las piezas individuales. El logro de este nivel más granular de recopilación de datos permite a Polamer Precision implementar continuamente mejoras incrementales en su programa de gestión de calidad (QMP).
Las ventajas de la internalización del proceso
Derek Waszczuk, vicepresidente de operaciones de Polamer Precision, explica: “Al incorporar nuestra operación de chapado a la empresa, hemos podido duplicar nuestra producción y reducir el plazo de entrega al eliminar la necesidad de enviar los productos a un proveedor externo.
“El estricto control de calidad es una faceta clave de nuestras operaciones. El sistema nos da la propiedad completa del proceso de fabricación y control de calidad, desde la materia prima hasta la entrega, lo que nos permite servir mejor a nuestros clientes.”
Para saber más sobre SIFCO ASC y sus soluciones, visite www.sifcoasc.com.
SIFCO ASC presenta una nueva técnica de galvanoplastia en el mercado: la galvanoplastia encapsulada
SIFCO ASC, el líder mundial de la galvanoplastia selectiva, ha sacado al mercado un nuevo método de revestimiento denominado revestimiento encapsulado, que combina la tecnología de la galvanoplastia selectiva y del revestimiento en tanque.
El nuevo proceso aprovecha lo mejor de las dos técnicas existentes para ofrecer una forma sostenible de chapar piezas complejas, circulares o axi-simétricas, como taladros profundos o zonas empotradas. Al ofrecer las mismas ventajas que el metalizado selectivo, el proceso minimiza el enmascaramiento, reduce la necesidad de sumergir toda la pieza, genera un mínimo de residuos y mantiene un ritmo de metalizado rápido.
Utilizando principios electroquímicos fundamentales y utillajes personalizados que se ajustan a la geometría de la zona que hay que revestir, la pieza se encapsula dentro de un accesorio sellado y la solución de revestimiento se dirige a través de un hueco en el utillaje, permitiendo que la solución fluya sobre el componente a gran velocidad. Debido a la naturaleza del método de revestimiento, el nuevo proceso es adecuado para múltiples sectores, desde la generación de energía y la industria hasta la electrónica y la industria aeroespacial.
Gracias a su enfoque único, el revestimiento encapsulado es más respetuoso con el medio ambiente que otros métodos de revestimiento, y ofrece importantes ventajas para la salud y la seguridad de los operarios y empleados. Además, el nuevo método ofrece un nivel de control del proceso, repetibilidad y trazabilidad que no puede lograrse con otros métodos de revestimiento, lo que proporciona al cliente un servicio seguro para los componentes críticos.
Patrick Kerampran, Director de Ingeniería de SIFCO ASC Francia, afirma: “Hemos identificado la necesidad de una solución que sea capaz de chapar un gran volumen de piezas complejas, sin dejar de utilizar el proceso de galvanoplastia selectiva. Nuestra nueva solución combina las ventajas de ambas tecnologías de metalizado líderes para satisfacer la demanda del mercado.”
“Al pasar a procesos menos intensivos en mano de obra, podemos reducir los costes de mano de obra y, al mismo tiempo, ofrecer una mayor eficiencia para el cliente final, una ventaja muy valiosa cuando se necesitan grandes volúmenes de componentes para el metalizado. Con beneficios adicionales que van desde procesos más limpios y un mayor control del proceso, el metalizado encapsulado permitirá a SIFCO ASC servir mejor a sus clientes y continuar liderando el mercado de la tecnología de metalizado”.
Para obtener más información sobre la mejor manera de revestir las zonas no visibles, el próximo seminario web de SIFCO ASC sobre revestimiento encapsulado cubrirá las ventajas de este enfoque único. El seminario web se celebra el martes 24 de agosto y los asistentes pueden inscribirse a través del enlace: https://bit.ly/3hqpHsC
Para obtener más información sobre la nueva oferta de revestimiento de SIFCO ASC, visite https://www.sifcoasc.com/explore-encapsulated-plating para descargar el documento técnico.
SIFCO ASC recibe la certificación ISO 14001:2015 de gestión medioambiental
Cleveland, OH, 17 de diciembre de 2020 – SIFCO ASC, los líderes mundiales de la galvanoplastia selectiva, ha recibido recientemente su certificado ISO 14001:2015, lo que demuestra su compromiso con la sostenibilidad medioambiental.
La norma ISO 14001:2015, reconocida internacionalmente, aborda diversos aspectos de la gestión medioambiental y reconoce a las empresas que identifican y controlan su efecto medioambiental en diversas áreas. SIFCO ASC completó su auditoría de fase 1 con la gestión de calidad de Smither, mostrando cómo sigue el marco de la norma, que abarca todo el ciclo de vida de los productos, y no sólo su producción.
SIFCO ASC cumplió los estrictos criterios de la norma adoptando medidas para reducir el consumo de energía en su sede central de Estados Unidos en Cleveland (Ohio). El ahorro se ha generado gracias a la reducción del uso de electricidad mediante el cambio a luces LED, la reducción de la cantidad de residuos peligrosos producidos, el control activo del uso de botellas y la cantidad de papel utilizado en toda la oficina.
Darrin Radatz, Director de Salud y Seguridad Medioambiental de SIFCO ASC, dijo: “Mantener voluntariamente un sistema de gestión de la calidad y el medio ambiente según las normas ISO nos ayuda a comprender cómo podemos minimizar nuestro impacto en el medio ambiente, cumplir la normativa gubernamental, mejorar continuamente y, sobre todo, ser lo más sostenibles posible.
“Una auditoría realizada hace 18 meses a nuestro sistema de gestión medioambiental reveló que ya habíamos realizado varios cambios positivos, como el uso de iluminación LED de bajo consumo, la reducción del uso de aire comprimido, el reciclaje de plástico y cartón, la reutilización de embalajes y la garantía de que todos los equipos eléctricos se apagan cuando no se utilizan. Desde esa auditoría, hemos introducido cambios adicionales en nuestra forma de operar, lo que ha llevado a SIFCO ASC a obtener la norma ISO 14001:2015 de gestión medioambiental.”
SIFCO ASC, una empresa de Quaker Houghton, ofrece soluciones de galvanoplastia selectiva prácticas y rentables para mejorar el rendimiento de las piezas y reducir los costes de fabricación mediante la protección contra la corrosión, el aumento de la resistencia al desgaste, el aumento de la dureza, la mejora de la conductividad, la antigripado y mucho más. Trabajando en sectores como el aeroespacial, el petróleo y el gas, la generación de energía, la industria general y la marina, por nombrar algunos, los servicios por contrato, las soluciones químicas y los equipos de SIFCO ASC se han utilizado durante más de 50 años tanto en componentes OEM como en piezas que requieren reacondicionamiento.
“Estamos encantados de que se nos reconozca por nuestros esfuerzos y es un testimonio de nuestro compromiso con la mejora de la eficiencia de nuestras operaciones y la mayor atención a nuestras credenciales medioambientales”, dijo Radatz. “Como parte de nuestro programa de mejora continua y de nuestra dedicación a la gestión medioambiental, nuestro objetivo es reducir aún más nuestro consumo de energía, el uso de plásticos y los residuos peligrosos generados por nuestros procesos químicos.”
Para más información sobre SIFCO ASC, visite www.sifcoasc.com.
La evolución de la automatización en la galvanoplastia selectiva
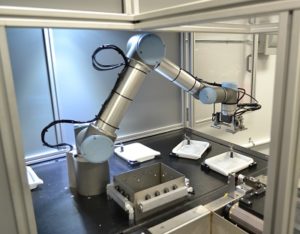
El revestimiento selectivo es un proceso bien establecido y fiable que ya se ha incluido en múltiples especificaciones aeroespaciales. No sólo supera los requisitos fundamentales de los procesos de fabricación, reparación y mantenimiento de aeronaves, sino que también proporciona un círculo completo de ventajas, como calidad, durabilidad, ahorro de costes, portabilidad y ahorro de tiempo.
Pero al automatizar el proceso de chapado selectivo, los operarios pueden revisar los datos capturados para determinar si la operación se ha realizado correctamente. Si se produce algún error o no se cumplen las normas de calidad, los operarios pueden revisar los datos y rastrear el error hasta su origen y asignar la acción correctiva adecuada, evitando que los errores se repitan, lo que mejora eficazmente la trazabilidad y la repetibilidad dentro del proceso. Además, la automatización reduce el riesgo ergonómico para el operario y también aumenta la capacidad disponible al permitir que los operarios cualificados se centren en los procesos empresariales principales.
Estas ventajas pueden verse claramente en la industria aeroespacial con el reciente y muy apreciado trabajo de SIFCO ASC con los principales fabricantes de motores de aviones y componentes de trenes de aterrizaje en el Reino Unido y Estados Unidos.
Para saber más sobre el trabajo realizado para los principales fabricantes de componentes aeronáuticos, lea el artículo completo en https://www.aero-mag.com/evolution-automated-plating/
SIFCO ASC se alinea para la demostración FABTECH 2021 de FAB to FINISH
SIFCO ASC mostrará su proceso de galvanoplastia selectiva en la edición de este año de FABTECH 2021 en el marco de la experiencia de producción FAB to FINISH de la feria. El taller en vivo ofrece a los asistentes la oportunidad de observar la producción de las piezas, desde la fabricación hasta el proceso de acabado, todo ello en la sala de exposiciones.
Coordinado por la Chemical Coaters Association International (CCAI), FAB to FINISH demostrará una variedad de técnicas de fabricación y acabado. Los procesos de producción expuestos incluyen el corte por láser, el curvado y el pretratamiento, el recubrimiento en polvo, el curado y, por último, el SIFCO Process®, la solución de galvanoplastia selectiva líder en el mundo de SIFCO ASC.
La galvanoplastia selectiva, que ofrece un nivel de portabilidad superior a los métodos de revestimiento rivales, será especialmente relevante para los asistentes que busquen mejorar la superficie de los componentes OEM, aplicar reparaciones permanentes o recuperar piezas desgastadas y mal mecanizadas. Estas técnicas de acabado superficial pueden realizarse sin necesidad de transportar la pieza a instalaciones externas.
Mark Meyer, Director de Ventas para América del Norte de SIFCO ASC, dijo: “Este año hemos querido ofrecer a los visitantes de FABTECH una experiencia realmente completa y memorable de lo que hacemos en SIFCO ASC. Tras pasar por los distintos talleres, los asistentes podrán acompañarnos en la fase final de la producción, donde podrán ver cómo chapamos el cobre mediante galvanoplastia selectiva. Lo mejor de todo es que podrán llevarse la pieza a casa como recuerdo”.
Los asistentes verán de primera mano la eficacia del proceso de galvanoplastia selectiva y las mínimas herramientas y equipos necesarios para llevar a cabo la galvanoplastia in situ, como grupos electrógenos, cables, ánodos, soluciones, bandejas y ventilación portátil.
Además, los representantes de SIFCO ASC estarán presentes en el evento para responder a cualquier pregunta sobre la galvanoplastia selectiva, al tiempo que hablarán de la oferta de servicios más amplia de SIFCO ASC, que abarca desde el nuevo método de galvanoplastia encapsulada y la automatización hasta el servicio por contrato y la formación esencial para cualquier industria.
La experiencia de producción FAB to FINISH comienza en las cabinas de corte y plegado por láser. A partir de ahí, los asistentes se dirigirán al pabellón de acabado, donde se limpiarán las piezas, listas para que el asistente pueda revestir el componente por sí mismo después de ver el proceso de curado. Por último, SIFCO ASC chapará la pieza con cobre mediante galvanoplastia selectiva.
SIFCO ASC es una empresa de Quaker Houghton y estará en el stand D45762. FABTECH tendrá lugar del 13 al 16 de septiembre de 2021 en McCormick Place, Chicago, Estados Unidos.
Para más información sobre SIFCO ASC, visite www.sifcoasc.com.
El proceso de aprobación de las reparaciones por cepillado en el sector aeroespacial: Una revisión
Cada día los cielos acogen miles de vuelos compuestos por aviones de pequeño y gran tamaño que transportan hasta 800 pasajeros a sus destinos deseados. A medida que aumenta el tamaño de la flota, se dispara la necesidad de revisiones periódicas, reparaciones y mantenimiento OEM.
Desde hace varias décadas, el cepillado selectivo es un proceso aprobado en el mantenimiento de aeronaves por la Administración Federal de Aviación (FAA) y los manuales de los fabricantes de motores y aeronaves OEM. El personal de mantenimiento de la aviación considera que el revestimiento con cepillos reduce los costes y el tiempo de inactividad, porque el proceso es portátil, fácil de usar, fiable, rápido y respetuoso con el medio ambiente.
Las aplicaciones aeroespaciales típicas incluyen:
- Protección contra la corrosión
- Prebraze
- Restauración dimensional
- Mejora de las propiedades de la superficie
- Reparación de componentes de aluminio
- Eliminación selectiva del cromo
Todos los procedimientos de reparación de aeronaves deben estar cubiertos por especificaciones o procedimientos de ingeniería aprobados. La primera especificación de la aviación comercial para el revestimiento con cepillos se redactó en 1956. En la actualidad, el revestimiento con cepillos selectivos está contemplado en más de 100 especificaciones aeronáuticas.
¿Cuál es el procedimiento adecuado para obtener una reparación de un componente de avión? En primer lugar, revise el manual de reparación*. En segundo lugar, hay que mantener abiertas las líneas de comunicación con los fabricantes y la FAA**. Las reparaciones legales que se realizan en las aeronaves civiles se llevan a cabo mediante instrucciones de:
- Manual de mantenimiento del fabricante
- Instrucciones para el mantenimiento de la aeronavegabilidad (preparadas por el fabricante)
- Procedimientos aprobados por la FAA
- Circular consultiva
- Reparación de ingeniería
El cepillado y el anodizado se han convertido en parte integrante del proceso de reparación, ya que se citan en numerosas publicaciones de procedimientos de reparación, prácticas estándar, especificaciones de procesos, manuales de reparación, boletines de servicio y especificaciones de fabricación. Los centros de reparación de la FAA que cuentan con la aprobación de la FAA con una calificación autorizada pueden realizar la reparación según los requisitos especificados.
En algunos casos, las reparaciones pueden variar con respecto al manual de revisión o mantenimiento, como el chapado con cepillo en lugar del chapado con tanque. Si bien el resultado final es comparativo, los medios para llegar a él son diferentes. En estos casos, es importante comunicarse con todas las partes para asegurarse de que la aplicación está escrita en la especificación aplicable. Una simple llamada telefónica al fabricante puede ser todo lo que se necesita para obtener la aprobación por escrito. Es esencial una buena comunicación con el fabricante.
Sin embargo, los nuevos procedimientos de reparación pueden encontrar cierta resistencia debido a los costes, la seguridad, los requisitos de prueba, la información de propiedad exclusiva u otras preocupaciones. Si la reparación es técnicamente correcta, se puede obtener un cambio de procedimiento:
Circular consultiva 43.13-1B de la FAA
Representante de ingeniería designado por la FAA (DER)
Aunque la FAA no tiene ninguna obligación con los fabricantes de equipos originales, suele consultar a un fabricante para obtener una opinión técnica, especialmente en el caso de los componentes críticos.
En resumen, el chapado con cepillos es un proceso ya aprobado por la FAA y los OEM. Para empezar a utilizarlo en sus componentes, consulte el manual de reparación para conocer el procedimiento adecuado. ¿Tiene algún cambio en el procedimiento? Póngase en contacto con el fabricante. ¿Tiene un nuevo procedimiento? Póngase en contacto con la FAA. Pronto el Proceso SIFCO® será conocido como un método aprobado para su uso en la industria aeroespacial.
Para obtener información sobre la acreditación de calidad de SIFCO ASC, haga clic aquí. Para obtener información sobre cómo se utiliza el revestimiento con cepillos en la industria aeroespacial, haga clic aquí.
*Para aplicaciones adecuadas.
**Buscar una fuente aprobada por la FAA para realizar la reparación.
Cómo mantenerse operativo durante las reparaciones de chapas
Cuando se trata de mantener turbinas y generadores en el sector de la generación de energía, el revestimiento selectivo ha sido durante mucho tiempo la solución de revestimiento elegida. Como proceso flexible, portátil y altamente eficaz, el metalizado selectivo ha demostrado ser una inversión rentable para los fabricantes de equipos originales y los especialistas en reparaciones, ya que permite crear un acabado robusto que cumple los requisitos de rendimiento óptimos para los componentes críticos.
Aquí, Mark Meyer explora cómo el chapado selectivo -el método preferido por líderes de la industria como Siemens, GE y MHPS- puede ayudar a mejorar la disponibilidad de los activos y el rendimiento de los mismos.
Al producir menos residuos y reducir significativamente el volumen de productos químicos necesarios (en comparación con el chapado en tanque), el chapado selectivo es un proceso altamente móvil e increíblemente flexible que permite realizar reparaciones in situ. Esto mejora la eficacia en cuanto a costes y tiempo de las reparaciones de los componentes críticos. Permite que las instalaciones permanezcan operativas y mejoren su rendimiento y disponibilidad de activos.
Rápido y eficaz cuando el tiempo importa
El metalizado selectivo permite a los operarios centrar con precisión el metalizado en zonas específicas de un componente, lo que permite metalizar las piezas in situ. Esto puede reducir drásticamente el tiempo de inactividad y minimizar los retrasos en la producción y el mantenimiento, lo que es especialmente beneficioso para las aplicaciones en las que las turbinas o los generadores deben volver al servicio en un momento crítico.
A diferencia del revestimiento de tanques, el revestimiento selectivo no requiere un amplio enmascaramiento ni dispositivos especiales para el revestimiento del componente. La duración de una operación de revestimiento viene determinada por el tamaño de la pieza y los requisitos de espesor. En los sistemas de metalización selectiva líderes en el mercado, los depósitos pueden ser metalizados a velocidades entre 30 y 60 veces más rápidas que la metalización convencional en tanques. El revestimiento selectivo también permite el revestimiento de zonas de las piezas que son demasiado grandes para caber en un tanque.
Las diferencias de rendimiento y coste que estos factores pueden suponer para el mantenimiento, la mejora o la reparación de componentes críticos pueden ser significativas.
Un proceso, múltiples revestimientos
El proceso de revestimiento selectivo es adecuado para reparar una variedad de componentes críticos de turbinas o generadores y puede utilizarse para una amplia gama de aplicaciones, como la mejora de la protección contra la corrosión, la resistencia al desgaste, la conductividad eléctrica y la mejora de la lubricidad, al tiempo que aumenta el rendimiento y la vida útil. Los yacimientos incluyen zinc-níquel, níquel, níquel-tungsteno, carburo de cobalto-cromo, plata, oro, platino y otros.
Eliminación de errores mediante la automatización
¿Sabía que, si bien el chapado selectivo puede llevarse a cabo manualmente, gracias a los avances en la tecnología de automatización, las instalaciones de reparación y los fabricantes pueden lograr ahora una calidad y consistencia aún mayores al eliminar los errores del operario y optimizar las propiedades del depósito? Con el uso de paquetes de potencia programables, los operadores pueden utilizar parámetros de revestimiento estandarizados que incluyen voltios, amperios y amperios-hora para obtener depósitos consistentes de componente a componente. Estos datos también pueden capturarse y almacenarse para un control de calidad sin fisuras.
Una alternativa probada
En el sector de la generación de energía, los técnicos e ingenieros disponen de múltiples opciones de reparación que pueden utilizarse en función del tamaño, la ubicación y los daños del componente. Sin embargo, cada proceso tiene sus desventajas cuando se compara con el chapado selectivo. Por ejemplo, un cliente preocupado por el presupuesto necesitaba cambiar el diámetro de los rodamientos de un bloque de empuje de 42,5 pulgadas. Se consideró la posibilidad de utilizar manguitos y rociadores de llama, pero los manguitos tienen limitaciones inherentes en un agujero con chavetas y los rociadores de llama se consideraron demasiado peligrosos.
Se utilizó el revestimiento con cepillo selectivo como alternativa eficiente en cuanto a costes y tiempo, superando las expectativas en todo el proceso.
Muchos en la industria de la generación de energía prefieren el chapado con cepillo in situ como una forma de evitar las marcas de la cremallera del chapado del tanque. Estos requieren inevitablemente un trabajo adicional de “retoque” tras el proceso de depósito, un método de reparación doble que requiere mucho tiempo y es ineficaz, y que puede evitarse con el uso del revestimiento selectivo.
Obtenga más información con el seminario web de SIFCO ASC
El 29 de enero de 2020 impartiremos un seminario web – Conducción de negocios: Maximizar los beneficios reduciendo el tiempo de inactividad de las turbinas. Creado específicamente para los directores de proyectos, ingenieros de procesos o de reparaciones, además de los especialistas en generadores y aquellos que participan en el mantenimiento, tratamiento y revestimiento de componentes críticos para el sector de la generación de energía. Este seminario web le apoyará en:
- Comprender los fundamentos del proceso de revestimiento selectivo
- Conocer las especificaciones industriales y comerciales que cumple el SIFCO Process®.
- Exploración de ejemplos reales de reparaciones y mejoras de componentes críticos
- Comprender las ventajas de la galvanoplastia selectiva frente a otros procesos de acabado superficial
Para inscribir su plaza, visite www.sifcoasc.com/conducting-business-webinar. Si desea más información sobre el revestimiento selectivo, visite www.sifcoasc.com.
Por qué el chapado selectivo evita que sus engranajes se detengan (Parte 1)
Los engranajes son una parte crucial de muchas máquinas, y si se desgastan y corroen sin posibilidad de reparación, puede ser un gasto costoso sustituirlos.
Las reparaciones pueden ser necesarias en dos etapas diferentes: fabricación y MRO.
Durante la fase de fabricación, a pesar de todos los centros de mecanizado modernos, las piezas pueden acabar mal mecanizadas, ya sea en el agujero, en los dientes o en el eje. El alcance de estos defectos dimensionales suele ser pequeño, pero el coste de refabricar toda la pieza sería prohibitivo.
Cuando están en funcionamiento, los engranajes suelen estar sometidos a entornos adversos, siendo problemas habituales el desgaste por corrosión o el funcionamiento diario en condiciones de polvo.
Con engranajes pequeños, el coste de capital de la sustitución de estos componentes en muchos casos será tolerable. Sin embargo, en los equipos de mayor tamaño, como la maquinaria de movimiento de tierras, industrial o marina, los ingenieros de mantenimiento no sólo deben tener en cuenta los gastos de capital. No sólo el coste de capital de los engranajes más grandes es mucho más alto, sino que también está el tiempo de inactividad de las máquinas fuera de servicio que puede hacer que el coste real de la sustitución de estos componentes sea extraordinariamente alto.
De hecho, el tiempo de inactividad es uno de los mayores costes a los que puede enfrentarse cualquier empresa. En Gran Bretaña, el impacto del tiempo de inactividad de las máquinas está costando a los fabricantes más de 180.000 millones de libras esterlinas cada año (The Manufacturer). El estudio, realizado por Oneserve, reveló que el 3% de todas las jornadas laborales se pierden anualmente en la industria manufacturera debido a fallos en la maquinaria. El 83% de los encuestados también afirma que sustituye las máquinas al menos una vez al año, lo que sin duda conlleva enormes implicaciones financieras y costes operativos.
Dicho esto, es crucial que los costes de mantenimiento se mantengan bajos, que los componentes de la maquinaria, como los engranajes, puedan mantenerse en servicio el mayor tiempo posible y que, en caso necesario, puedan repararse de forma rápida y eficaz.
El cepillado, o galvanoplastia selectiva, es una forma rentable y probada de devolver a los engranajes sus especificaciones originales y ayudar a prolongar su vida útil.
El cepillado, o galvanoplastia selectiva, es una forma rentable y probada de devolver a los engranajes sus especificaciones originales y ayudar a prolongar su vida útil.
El revestimiento puede servir para una variedad de propósitos, como la reparación de un defecto localizado o para devolver el diámetro interior (DI) o el diámetro exterior (DE) a su tamaño. El chapado también puede mejorar la resistencia al desgaste o a la corrosión exactamente donde se necesita, incluso en piezas nuevas en las que sería prohibitivo fabricar toda la pieza con un material más resistente.
Cuando se evalúan las piezas para su reparación, siempre es importante tener en cuenta el tamaño y la ubicación de la reparación requerida, y la cantidad de material que hay que chapar, ya que esto determinará si el chapado selectivo es apropiado o no.
Las mujeres en STEM: iluminando a Danijela Milosevic-Popovich
El Mes de la Historia de la Mujer, que tiene lugar del 1 al 31 de marzo de cada año, se propone reconocer y celebrar los logros de las mujeres de todo el mundo. Aunque es importante reconocer los méritos de todas las mujeres, nos centramos en las que trabajan en STEM (ciencia, tecnología, ingeniería y matemáticas) y hemos destacado a Danijela Milosevic-Popovich, nuestra Directora de Investigación y Desarrollo.
Desde hablar de cómo eliminar el techo de cristal para las mujeres en la ingeniería, hasta cambiar el futuro de la galvanoplastia, descubrimos lo que inspira a Danijela, y cómo se esfuerza por crear un futuro mejor para ella y otras mujeres en STEM.
Ciencias y matemáticas: los fundamentos de STEM
Danijela sabía que quería trabajar en un campo STEM desde que era joven: su pasión por las ciencias y las matemáticas empezó en la escuela primaria. Le encantaba el reto de descifrar ecuaciones y aprender teorías, y desde muy pronto supo que tener una formación científica le proporcionaría una base sólida independientemente de la carrera que siguiera.
Su padre -su mayor animador e inspiración- siempre la motivó a avanzar en su educación y a luchar por su independencia. Al crecer en los Balcanes, no era habitual que las chicas fueran a la universidad y, aunque su apoyo a que siguiera estudiando se consideraba un tabú, nunca dejó que las críticas la distrajeran.
Danijela se da cuenta de lo mucho que su infancia y su educación marcaron su carrera. Las ciencias y las matemáticas ayudan a Danijela a pensar de forma más crítica. Aborda cada problema sabiendo que hay un proceso lógico que seguir. También cuestiona los factores críticos asociados a la resolución. Ella dijo:
“Creo que una sólida formación en STEM ayuda a entrenar el cerebro para pensar de forma más crítica. La intuición y el pensamiento crítico juntos crean la tormenta perfecta para la resolución de problemas y creo que las matemáticas y la ciencia son bloques de construcción clave para perfeccionar este proceso.”
Educación: el pasaporte para el futuro
Con una licenciatura y dos másteres en su haber, Danijela sabe lo importantes que son la educación y las cualificaciones para cualquiera que quiera trabajar en STEM. Aunque todavía queda mucho camino por recorrer para cerrar la brecha de mujeres que trabajan en estos campos, el número de mujeres que obtienen títulos STEM cada año ha aumentado en más de 50.000 en la última década.
Cambiando el panorama de la galvanoplastia
Cuando se le pregunta por su función diaria en SIFCO ASC, Danijela se ilumina al hablar de todas las áreas en las que participa.
“Cada día aporta algo nuevo. Mi función abarca mucho más que las actividades tradicionales de I+D: es multifacética y me mantiene alerta. Mi departamento y yo somos los depositarios de los conocimientos técnicos, lo que, en última instancia, hace crecer las capacidades de la base de conocimientos de nuestras líneas de productos existentes y el desarrollo de nuevas aplicaciones, soluciones de revestimiento y tecnología.”
Gracias a esta investigación y a su base de conocimientos, Danijela y su equipo están cambiando poco a poco la percepción del revestimiento con cepillos. Avances como los grupos de potencia programables y la automatización del proceso no sólo han revolucionado la forma de realizar la galvanoplastia, sino que han proporcionado a los ingenieros de reparación un control aún mayor.
“A medida que hemos desarrollado diversas aplicaciones de metalizado, hemos podido introducir más controles en las fases de procesamiento. Como resultado, hemos perfeccionado los parámetros del proceso de metalizado para proporcionar características de depósito repetibles y controlables para un proceso que tradicionalmente es realizado manualmente por un operario. Este nivel de control nos ha impulsado a seguir desarrollando aplicaciones y equipos de metalizado semiautomáticos y totalmente automatizados, así como a alejarnos del tradicional metalizado por cepillado mediante el desarrollo de tecnologías de metalizado encapsulado”.
Crear un futuro más seguro y sostenible
No es sólo el proceso de galvanoplastia el que está sintiendo el impacto: esta investigación y desarrollo está allanando el camino hacia un futuro mucho más seguro y sostenible para los mecánicos de reparación y el medio ambiente. En colaboración con un equipo de ingenieros, Danjiela desarrolla alternativas de revestimiento de cepillos que cumplen con REACH.
Por ejemplo, el cadmio y el cromo duro son comúnmente utilizados por los ingenieros de reparación de mantenimiento que llevan a cabo reparaciones de componentes para una amplia gama de industrias debido a su mayor resistencia al desgaste, dureza de la superficie y durabilidad. Sin embargo, la exposición a ambos metales en su estado compuesto puede ser increíblemente perjudicial tanto para los técnicos de revestimiento como para el público en general.
Las acciones de Danijela y su equipo están empezando a tener profundas consecuencias en la industria del chapado y en el planeta. Mediante la exploración, el análisis y el desarrollo, SIFCO ASC ha desarrollado soluciones de revestimiento con cepillos que pretenden sustituir al cadmio y al cromo en el futuro.
“En estos momentos, no existe una solución única para sustituir el cadmio o el cromo, por lo que nos centramos en fabricar soluciones como el ZnNi (Zinc-Níquel) como alternativas al cadmio, y soluciones MMC (compuesto de matriz metálica) para las alternativas al cromo.”
El reto de ser mujer en STEM
Cuando se le pregunta “¿cuáles son los retos de ser mujer en STEM?”, Danijela dice que son las mismas barreras estereotipadas que se han interiorizado durante varias décadas. Habla del sesgo inconsciente por el que tanto los hombres como las mujeres están condicionados a pensar que los hombres son más inquisitivos, están más motivados y son más responsables. En consecuencia, las mujeres tienen que trabajar más.
Sin embargo, piensa que si cambiamos la narrativa, tal vez podamos eliminar el techo de cristal tanto para las mujeres como para las minorías en STEM, si empezamos a celebrar sus logros, en lugar de los retos a los que se enfrentan. Ella dice:
“Cada mujer en un campo STEM tiene por delante un conjunto único de desafíos que ningún hombre tendrá que experimentar. Me gustaría destacar los logros de las mujeres en STEM históricamente para que podamos establecer un marco para el reconocimiento continuo de nuestras niñas a medida que se convierten en mujeres y cambian el mundo junto a sus colegas masculinos.”
Para cualquier mujer que quiera avanzar en su carrera en STEM, ya sea más joven o mayor, Danijela dice que creer en uno mismo y encontrar un mentor que te aconseje y te empuje fuera de tu zona de confort es lo mejor que puedes hacer.
“Hubo una reunión de alto nivel a la que asistieron cuatro niveles de directivos, lo que resultaba bastante abrumador para una mujer joven, especialmente cuando la mayoría de los asistentes eran hombres. Repasé mi presentación con mi jefe de antemano, y me dijo que se reuniría conmigo allí. Pero no apareció. Sobreviví a la reunión, me acerqué a su despacho y le pregunté por qué no se había presentado. Me dijo que “no quería quitarme el protagonismo”, que “no quería que el resto de la sala viera a un HOMBRE detrás de mí”. Me enseñó que era capaz de valerme por mí misma y que nunca debía sentirme inferior, independientemente de quién estuviera en mi compañía”.
Para más información sobre la investigación de Danijela y las soluciones de revestimiento de SIFCO ASC, visite https://www.sifcoasc.com/
Por qué el chapado selectivo evita que sus engranajes se detengan (Parte 2)
Construir capas sin comprometer la resistencia, la durabilidad y las especificaciones del equipo
Los engranajes utilizados en grandes aplicaciones son caros de sustituir si se dañan o desgastan.
En muchos casos, el revestimiento con cepillos puede devolver los componentes de los engranajes a su especificación nominal y, en algunos casos, incluso superar el rendimiento del material original.
El níquel es uno de los materiales de revestimiento más utilizados en las reparaciones. Otros materiales, como el cobalto, también son populares, mientras que ciertas aleaciones, como las de níquel-tungsteno o las de níquel-cobalto, pueden proporcionar sus propias propiedades únicas. Con una selección adecuada de los parámetros de deposición, se puede influir en la estructura del grano del níquel para obtener las propiedades deseadas, como la dureza y la resistencia a la corrosión, lo que le permite soportar el funcionamiento diario al que se someten los engranajes.
En el caso de los engranajes, las reparaciones más comunes son los ejes, los muñones de los cojinetes y los orificios. En las circunstancias adecuadas, también se puede considerar el daño localizado en los dientes. En el caso de los engranajes que van a estar en un entorno corrosivo, los orificios y las superficies exteriores mecanizadas que no se pueden pintar también se chapan cuando son nuevos para proporcionarles resistencia a la corrosión.
La galvanoplastia selectiva in situ reduce los costes
Otra consideración a la que se enfrentan los ingenieros a la hora de reparar engranajes es cómo se puede realizar el mantenimiento incurriendo en el menor coste posible. Estos pueden empezar a aumentar a través de los gastos directamente asociados, como el envío del engranaje a un taller, el desmontaje y montaje del engranaje, y la propia reparación. Además, hay que tener en cuenta los costes indirectos, como los trastornos, el tiempo de inactividad y la pérdida de productividad.
A menudo, los engranajes que son demasiado grandes para reemplazarlos simplemente también son demasiado grandes para desmontarlos fácilmente y demasiado poco prácticos y costosos para enviarlos a talleres externos para su reparación. El tiempo de inactividad también se prolonga, debido a la necesidad de desmontar el equipo y la maquinaria, y esperar a que se repare, se envíe de vuelta y se vuelva a montar.
El cepillado supera estos obstáculos. En muchos casos, los técnicos pueden evaluar los daños en los engranajes y realizar las reparaciones in situ.
Este fue el caso de la reparación del piñón de la excavadora de arrastre. Sobre la reparación, Dave Niederhelman, metalúrgico jefe de Horsburgh & Scott Co. dijo “SIFCO ASC es un socio bien establecido de Horsburgh & Scott y su capacidad para trabajar in situ es muy atractiva. A lo largo de los años nos han ayudado a encontrar las formas más eficientes de reparar y mantener los equipos de nuestros clientes y esto ha supuesto un ahorro de miles de dólares, horas de inactividad y tiempo de mano de obra.
“En esta aplicación, el SIFCO Process® ha prolongado la vida útil del engranaje y ha mejorado el índice de fallos gracias a la naturaleza del recubrimiento de níquel del gorrón. El coste de fabricación y material para sustituir el engranaje habría sido desorbitado en comparación, además de provocar semanas de inactividad.”