Schwimmende Windturbinen – die Zukunft der erneuerbaren Energien
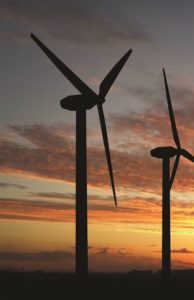
Bis zum Ende des Jahrzehnts sollen bis zu 38.000 Megawatt an Windturbinen auf dem Meeresboden installiert werden; die schottische Grafschaft Aberdeen könnte schon Ende des Jahres davon profitieren. Schottland, das sich als führende Nation bei der Innovation und dem Einsatz schwimmender Offshore-Windkraftanlagen” etabliert hat, hat bereits Baugenehmigungen für 92 Megawatt Kapazität von mehreren Entwicklern erneuerbarer Energien erteilt.
Die norwegische Firma Statoil war die erste, die im Mai 2016 die Genehmigung erhielt; die größte Anlage ist die schottische Kincardine Offshore Windfarm Ltd. die im März 2017 die Genehmigung erhielt. Kincardine wird etwa 10 Meilen vor der Küste von Aberdeen acht Sechs-Megawatt-Turbinen errichten, die 56.000 Haushalte mit Strom versorgen können.
Weitere schwimmende Windparkprojekte sind:
- Das irische Unternehmen Gaelectric Holdings Plc. und das französische Unternehmen Ideol SAS für irische Gewässer zugelassen.
- Das schwedische Unternehmen Hexicon AB vor der Küste von Inverness
- Die japanische Toda Corp. vor der Küste von Nagasaki
Diese aufstrebende Technologie wurde von der Offshore-Ölindustrie inspiriert, deren Bohrinseln seit Jahrzehnten den starken Winden und den Tiefen des Ozeans trotzen. Die schwimmenden Turbinen werden weniger Kosten und Material erfordern als herkömmliche Offshore-Turbinen, die bis zu einer Tiefe von 40 Metern oder mehr auf dem Meeresboden versenkt werden. Die Basis jeder Turbine schwimmt auf einem Stahlrohr, das einen Ballast enthält, und wird zur Unterstützung am Meeresboden befestigt.
An der schottischen Küste wehen einige der stärksten Winde, was sie zu einem idealen Standort für die Windparks macht. Doch die stürmischen Winde und das Meerwasser schaffen eine extrem korrosive Umgebung. Die Oberflächenbeschaffenheit von Opferbeschichtungen und verschleißfesten Werkstoffen für Turbinenwellen kann die Lebensdauer der Anlagen verlängern und die Ausschussrate verringern. Mit bewährten Ergebnissen aus der Offshore-Öl- und -Gasindustrie, bei denen das SIFCO-Verfahren für die Vor-Ort-Galvanisierung von Zapfenwellen und Lagergehäusen eingesetzt wird, können Reparaturen innerhalb einer Betriebsschicht abgeschlossen werden, wodurch die Turbinen länger in Betrieb bleiben.
Der Erfolg dieser Projekte ist von entscheidender Bedeutung, da Inseln mit weniger Ressourcen und Landmasse für die Deckung ihres Energiebedarfs auf Offshore-Windparks angewiesen sein könnten. Schottland und die Entwickler setzen auf das Fachwissen, das sie bei der Arbeit in der Offshore-Öl- und -Gasindustrie und in anderen Meeresumgebungen erworben haben, um saubere Energie zu erzeugen und ihr Ziel zu erreichen, bis 2030 die Hälfte der gesamten Energie aus erneuerbaren Quellen zu erzeugen.
Da der Ölmarkt rückläufig ist und die verfügbaren Flächen und Ressourcen immer knapper werden, stellt die Offshore-Windenergie eine vielversprechende Energielösung dar.
Weitere Informationen über das SIFCO-Verfahren und selektive Beschichtungsreparaturen erhalten Sie unter info@sifcoasc.com oder 800-765-4131.
Verlängerte Lebensdauer: Wie Ihre Öl- und Gasanlagen von einer Bürstenbeschichtung profitieren können
In der Öl- und Gasindustrie arbeiten die Geräte in rauen Umgebungen. Bauteile müssen Verschleiß, Korrosion, Temperatur- und Druckschwankungen standhalten, und die Betreiber benötigen Reparaturlösungen, die in kürzester Zeit durchgeführt werden können – mit hervorragenden Ergebnissen, die die Bauteile vor weiteren Schäden schützen.
SIFCO ASC hat ein Verfahren perfektioniert, mit dem große Komponenten wie BOP-Montageteile, Rohraufhängungskörper, Innendorne, Zylinder, Gehäuse, Steigrohrverbindungen und mehr repariert werden können. Einige davon ohne die Notwendigkeit einer Demontage.
Das SIFCO-Verfahren® der selektiven Beschichtung ist einzigartig. Es handelt sich um eine portabel Methode zur Galvanisierung örtlich begrenzter Bereiche ohne Einsatz eines Tauchbeckens. Die Abscheidungen wird auf abgenutzte oder beschädigte Bereiche aufgetragen, um die Größe zu ändern, zu reparieren oder die Leistung des Bauteils zu verbessern. Die extrem haftenden Schichten werden gleichmäßig und präzise aufgetragen, so dass in einigen Fällen eine Nachbearbeitung überflüssig ist. Darüber hinaus verfügen die erfahrenen und qualifizierten Mitarbeiter von SIFCO ASC über Zertifizierungen für die Arbeit auf Ölplattformen, so dass sie bei Bedarf schnell eingesetzt werden können.
Der SIFCO Process® ist in der Öl- und Gasindustrie hoch angesehen und wird bei vielen OEM- und Reparaturanwendungen eingesetzt. Alle Abscheidungenen werden unter strikter Einhaltung aller Spezifikationen und Qualitätsanforderungen aufgebracht. Das Verfahren erfüllt bereits die Spezifikationen von FMC, GE Oil & Gas, Halliburton, Schlumberger, Tenaris-Hydril, Vallourec und VAM.
SIFCO ASC ist in der Lage, die Industrie zu unterstützen, die Korrosionsgefahr zu verringern und gleichzeitig die wichtigsten Herausforderungen zu meistern, nämlich die Lebensdauer der Anlagen zu verlängern, Ausfallzeiten zu reduzieren und Betriebskosten zu senken.
Wenn Sie die Lebensdauer Ihrer Anlagen verlängern möchten oder weitere Informationen über unsere Öl- und Gasdienstleistungen wünschen, besuchen Sie unsere Website. Kontaktieren Sie uns noch heute unter 800-765-4131 oder info@sifcoasc.com
Sicherstellung ordnungsgemäßer Beschichtungsbedingungen unter direkter Kontrolle des Bedieners
In früheren Blogs haben wir bestimmte Bedingungen für die Bürstenbeschichtung behandelt, auf die der Bediener direkten Einfluss hat, um eine qualitativ hochwertige Abscheidung zu gewährleisten, wie z. B. die Geschwindigkeit zwischen Anode und Kathode und die Beschichtungstemperatur. Insgesamt hat der Bediener sechs Bedingungen für das Bürstenplattieren unter seiner direkten Kontrolle. Neben der Geschwindigkeit und der Temperatur sind dies die Anodenabdeckung, die Spannung, das Nachfüllen der Lösung und die Kontaktfläche.
Anodenabdeckung
Die Anodenabdeckung wirkt sich direkt auf die Qualität der Abscheidungen aus. Die Verwendung des richtigen Abdeckmaterials führt zu einer optimalen Abscheidungensqualität, Adhäsion und Kohäsion. Aufgrund jahrelanger Forschung und Tests gibt SIFCO ASC Empfehlungen für das richtige Abdeckmaterial für jede angebotene Lösung. Um das beste Abdeckungsmaterial für Ihre Anwendung zu bestimmen, lesen Sie das technische Datenblatt der Lösung.
Wiederauffüllung der Lösung
Die Aufrechterhaltung einer ausreichenden Menge an Beschichtungslösung auf dem Werkstück ist ebenfalls ein wichtiger kontrollierbarer Faktor. Bei der Verwendung der Lösung werden die Metallionen abgereichert. Das Auffüllen mit frischer Lösung ist wichtig, um die gewünschten Abscheidungenseigenschaften zu erhalten. Achten Sie darauf, die Lösung schnell genug zu pumpen oder oft genug zu tauchen, damit die Metallionen im Arbeitsbereich für das gesamte verwendete Lösungsvolumen repräsentativ bleiben.
Kontaktbereich
Eine gute Schicht wird so schnell wie möglich aufgetragen, wenn die Kontaktfläche zwischen dem Beschichtungswerkzeug und dem Werkstück optimal ist. Die optimale Kontaktfläche (OCA) ist die bestmögliche Kontaktfläche, die unter Berücksichtigung der Geometrie der zu beschichtenden Oberfläche, der maximalen Stromstärke des Netzteils und der durchschnittlichen Stromdichte der verwendeten Beschichtungslösung erreicht werden kann.
Die richtige Auswahl oder Konstruktion des Beschichtungswerkzeugs ist der erste Schritt zur Erzielung der richtigen Kontaktfläche. Das Instrument muss jedoch richtig eingesetzt werden:
Halten Sie das Werkzeug auf der zu beschichtenden Fläche.
Halten Sie das Werkzeug in festem, flachen Kontakt mit der Fläche.
SIFCO ASC-Standardwerkzeuge sind für die effiziente Vorbereitung und Beschichtung von Teilen unterschiedlichster Größe und Form erhältlich. Standardwerkzeuge können ausgewählt werden, wenn sie die folgenden Anforderungen erfüllen:
Vorbereitende Werkzeuge
Bedecken Sie mindestens 10 % der zu beschichtenden Fläche, wenn möglich.
Abdeckung in voller Länge.
Beschichtungswerkzeuge
Sorgen Sie für eine ausreichende Kontaktfläche.
Abdeckung in voller Länge.
Bei Bedarf kann die Lösung gepumpt werden.
Spannung
Die Spannung ist die letzte und am einfachsten zu kontrollierende Bedingung für die Beschichtung; sie erfordert schnelle, kleine Änderungen, die mit dem Spannungsregler vorgenommen werden. Jede Lösung wird innerhalb eines bestimmten Spannungsbereichs verwendet. Der relativ breite Spannungsbereich ist nach der Größe des Galvanisierwerkzeugs unterteilt.
Verwenden Sie den niedrigeren Spannungsbereich von 6 bis 13, wenn Sie kleine Werkzeuge verwenden und die Beschichtungsbedingungen ungünstig sind, z. B. wenn es schwierig ist, eine optimale Anoden-Kathoden-Geschwindigkeit zu erreichen, oder wenn Sie die Lösung eintauchen, anstatt eine Pumpe zu verwenden. Verwenden Sie den höheren Spannungsbereich von 13 bis 20, wenn Sie größere Werkzeuge verwenden und die Beschichtungsbedingungen günstig sind.
Durch die Kontrolle aller sechs Bedingungen für das Bürstenplattieren kann der Bediener eine hochwertige Abscheidungen mit hervorragender Haftung garantieren. Wenn Sie ein hohes Auftragsvolumen haben, sollten Sie eine Automatisierung in Betracht ziehen. In unserem Blog “Verbesserte Prozessfähigkeiten durch Automatisierung der selektiven Beschichtung” erörtern wir, wie die Automatisierung die Aufgaben des Bedieners um das Dreifache reduzieren kann. Mit einem automatisierten System werden die Schwankungen von Bediener zu Bediener eliminiert, da die Teileplatzierung, die Bewegung und der Druck bei jedem Teil gleich sind.
Wenn Sie Fragen zur Kontrolle der Beschichtungsbedingungen haben, wenden Sie sich bitte an unsere technische Serviceabteilung unter 800-765-4131 oder info@sifcoasc.com.
Technik für den Weihnachtsmannschlitten
Der folgende Blog ist ein Gastbeitrag von Surface Technology
In wenigen Tagen wird der Weihnachtsmann mit seinem berühmten roten Schlitten vom Nordpol aus aufbrechen. Beladen mit den diesjährigen Must-Haves Hatchimals und Star Wars wird er in der Nacht auf Heiligabend 317 Millionen Meilen über Ozeane und Kontinente reisen.
Mit einer Mischung aus Keksen, heißem Kakao und Karotten haben der Weihnachtsmann und seine Rentiere eine große Aufgabe zu bewältigen, um sicherzustellen, dass Millionen von Kindern auf der ganzen Welt zu Weihnachten ihre Geschenke erhalten.
Wir dachten uns, wir versuchen, die Oberflächentechnik zu verstehen, die erforderlich ist, damit der Weihnachtsmann und seine Rentiere ihre epische jährliche Mission erfüllen können.
Leider liegen uns keine Informationen aus dem geheimnisumwitterten Forschungs- und Entwicklungszentrum von Elf vor – dem zweifellos bedeutendsten der Welt -, aber wir haben uns mit Hilfe unseres eigenen technischen Teams Gedanken über die besonderen Anforderungen an den Schlitten des Weihnachtsmannes gemacht und einen Überblick über die möglichen Beschichtungen gegeben, die verwendet werden könnten.
Der Schlitten
Da der Weihnachtsmann nur 32 Stunden Zeit hat, um alle seine Lieferungen zu erledigen, ist Schnelligkeit das A und O für ihn. Es gibt viele Theorien darüber, wie der Schlitten mit 0,97 Prozent der Lichtgeschwindigkeit angetrieben wird – von Rentieren, die denselben Ernährungsberater haben wie die russische Olympiamannschaft 2012, bis hin zum Raketenantrieb.
Was wir jedoch wissen, ist, dass eine Beschichtung, die bei hohen Temperaturen effektiv funktioniert, wichtig sein wird. Keramische Beschichtungen, wie sie die NASA für ihre Space Shuttles verwendet, sind eine praktikable Option für die Karosserieteile des Schlittens.
Thermisches Spritzen, wie HVOF kann auch für alle beweglichen Komponenten verwendet werden, z. B. für Turbinenkomponenten (bei Raketenantrieben), da es bei hohen Temperaturen eingesetzt werden kann und einen besseren Schutz gegen Verschleiß, Korrosion, Ermüdung und Oxidation bei hohen Temperaturen bietet – das Letzte, was der Weihnachtsmann bei einem so engen Zeitplan gebrauchen kann, ist eine mechanische Störung.
Schlittenkufen
Bei so vielen Lieferungen werden die Kufen am Fuß des Weihnachtsmannschlittens Millionen von Landungen und Starts absolvieren. Ein zerbrochenes Spielzeug ist am Weihnachtsmorgen einfach nicht gut, daher ist eine sanfte Landung unerlässlich.
Wir vermuten, dass in der Elfenwerkstatt jedes Jahr selektive Beschichtungen verwendet werden, um sicherzustellen, dass die Kufen des Weihnachtsmanns gewartet und für den Weihnachtsstart bereit sind. Mit dem SIFCO Process® kann Nickel oder Kadmium verwendet werden, um abgenutzte oder abgeplatzte Stellen auf den Kufen neu zu beschichten. Außerdem ist das Verfahren FAA-zugelassen, so dass der Weihnachtsmann nicht auf der schwarzen Liste der Federal Aviation Authority steht.
Bremsen
Wir gehen davon aus, dass die Rentiere den Schlitten an jedem Absetzpunkt zum Stehen bringen, aber für ein bisschen mehr Bremskraft haben sich die Elfen des Weihnachtsmanns vielleicht für ein mechanisches Bremssystem entschieden. Eine Kombination aus Zinklegierung und Pulverbeschichtung (natürlich in RAL 3020) oder vielleicht sogar Keramikbeschichtung könnte dafür sorgen, dass der Weihnachtsmann keinen Halt macht.
Klimatisierung
Auf seiner Reise über den Himmel von Afghanistan bis Simbabwe – und 194 Ländern dazwischen – wird der Weihnachtsmann Temperaturen von unter Null bis über 95 Grad ausgesetzt sein.
Wir gehen davon aus, dass der Anzug des Weihnachtsmanns aus den besten Materialien Lapplands hergestellt wurde, um sowohl Wärme als auch Atmungsaktivität zu gewährleisten. Für zusätzlichen Komfort, insbesondere in heißen Klimazonen, haben die Elfen den Schlitten des Weihnachtsmanns vielleicht mit einer Klimaanlage ausgestattet.
Während Surface Technology, SIFCO ASC und Ultraseal Dienstleistungen für viele aufregende Konstruktions- und Fertigungsprojekte anbieten, wird die Antwort auf die Frage, wie der Weihnachtsmann und seine Rentiere all die Geschenke am Weihnachtsabend ausliefern, ein weiteres Jahr lang ein Geheimnis bleiben müssen.
Wir wünschen allen unseren Kunden in aller Welt ein frohes Weihnachtsfest und ein erfolgreiches neues Jahr.
Entdecken Sie die Effizienz von Reparaturen in der Luft- und Raumfahrt mit einem Webinar
Wir bei SIFCO ASC wissen, dass das Erreichen eines höheren Effizienzniveaus vielleicht eine der größten Herausforderungen für viele unserer Kunden ist. Für die Luft- und Raumfahrtindustrie, die einen Nachfrageschub im kommerziellen Sektor erlebt, ist Effizienz sogar noch wichtiger. Kombiniert man diese Herausforderung mit den gesetzlichen Bestimmungen, die die Verwendung von Chemikalien wie Cadmium regeln, so stehen die Unternehmen der Branche vor einem schwierigen Umfeld.
Kostenlose Teilnahme am Webinar: Bürstenbeschichtung und Anodisierung für die Luft- und Raumfahrt
Deshalb veranstaltet SIFCO ASC ein kostenloses Webinar, an dem Sie teilnehmen können. Unter der Leitung von Danijela Milosevic-Popovich – SIFCO ASC’s Research and Development Manager – bietet Spec’d In: Brush Plating & Anodizing for Aerospace wird fachkundige Informationen und Ratschläge für Hersteller in der Luft- und Raumfahrtindustrie bieten.
Das Webinar soll Einblicke in die Bewältigung der Herausforderungen geben, denen sich Hersteller und Betreiber heute gegenübersehen, und den Teilnehmern helfen, die selektiven Beschichtungs- und Eloxalverfahren zu verstehen und zu erkennen, wie sie die effizienten Reparaturmöglichkeiten für Luft- und Raumfahrtkomponenten verbessern.
Die Vorteile der selektiven Beschichtung gegenüber der Tankbeschichtung
sagte Danijela: “Unser Webinar soll den Teilnehmern einen fachkundigen Einblick in den Einsatz von selektiver Beschichtung und Eloxierung geben und aufzeigen, wie diese Verfahren zu mehr Effizienz in der Lieferkette der Luft- und Raumfahrt beitragen. Die Verfahren sind bereits in Überholungs- und Standardhandbüchern spezifiziert. In diesem Webinar geht es darum, wann und warum diese Verfahren gegenüber Alternativen wie der Tankbeschichtung eingesetzt werden sollten. Wir werden auch Beispiele aus der Praxis vorstellen, die die Zeit- und Kosteneinsparungen im Zusammenhang mit den Prozessen aufzeigen und zeigen, wie Kunden die Automatisierung nutzen können, um die Qualität und Konsistenz ihrer Beschichtungsprozesse zu verbessern.
Mehr Effizienz für die Luft- und Raumfahrt
“Die Luft- und Raumfahrtindustrie erlebt derzeit eine spannende und zugleich herausfordernde Zeit. Die Branche befindet sich in einer äußerst dynamischen Phase mit steigender Nachfrage, was jedoch eine Belastung für die Hersteller in der gesamten Lieferkette darstellt, während der MRO-Markt unter erhöhtem Druck steht, Flugzeuge so lange wie möglich in Betrieb zu halten. Unser Webinar wird den Herstellern helfen zu verstehen, wie sie ihre Effizienz maximieren können, was sie wettbewerbsfähiger macht und das Qualitätsniveau in der gesamten Branche anhebt.”
Auf der Suche nach der richtigen Defektreparatur
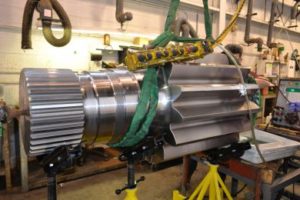
In der Bergbauindustrie sind Ersatzteile und Komponenten für industrielle Ausrüstungen aufgrund ihres Umfangs, ihrer Kosten und ihrer Vorlaufzeit in der Regel nicht vorrätig bzw. nicht ohne weiteres erhältlich. Die Betreiber brauchen also ein rechtzeitiges Verfahren, um ihre Komponenten intern zu reparieren, oder sie riskieren zusätzliche Kosten durch verlorene Arbeitsstunden und längere Ausfallzeiten.
Dies war der Fall bei einem Getriebehersteller aus Cleveland, Ohio, als eine Reparatur am Ritzel eines Schürfkübelbaggers erforderlich war. Das Ritzel ist Teil einer ganzen Getriebebaugruppe, und wenn es nicht regelmäßig gewartet wird, kann Schmiermittel aus der Dichtung austreten, was dazu führt, dass das Lager festsitzt und sich mit der Welle verbindet. Als dies geschah, wurde Horsburgh & Scott Co. damit beauftragt, das Getriebe und schließlich den Kran wieder funktionsfähig zu machen.
Als das festgefressene Lager entfernt wurde, wurde auch überschüssiges Material vom Zapfen entfernt, was zu einer Furche in der Oberfläche führte.
Herkömmliche Reparaturtechniken wie Schweißen, Ummanteln und Metallspritzen können aufgrund der Demontage- und Versandzeit vier bis sechs Wochen dauern, was zu längeren Ausfallzeiten führt und zudem kostspielig ist.
Das betreffende Lager hatte eine Furche von 0,030″ Tiefe, 0,75″ Breite und 12″ Länge, also 0,012″ Untermaß. Bei der selektiven Beschichtung werden Defekte in der Regel mit einer oder mehreren Kupferschichten repariert und dann mit einer verschleißfesten Schicht überzogen, die gute Trenn- oder Benetzungseigenschaften aufweist. In diesem Fall wurde der Lagerzapfen zunächst mit einer 0,001″ dicken Kupferschicht überzogen und dann für die Reparatur des Fehlers abgeklebt. Die Anode, die zum Füllen des Defekts verwendet wurde, bedeckte die gesamte Länge der Fuge, die mit drei Lagen Kupfer gefüllt und dazwischen handgearbeitet wurde. Die letzte Schicht wurde bündig abgerichtet und dann mit einer 0,006″ dicken Nickelschicht mit einem ID-Plattierer beschichtet.
Durch den Einsatz des SIFCO Process® war Horsburgh and Scott Co. nicht nur in der Lage, den Kran mit minimaler Ausfallzeit wieder in Betrieb zu nehmen, sondern konnte auch die Zeit zwischen den Ausfällen verbessern und im Vergleich zu alternativen Reparaturmethoden erhebliche Kosten einsparen.
Der SIFCO Process® kann auch in anderen Bereichen der Bergbauindustrie eingesetzt werden:
GELÄNDEGÄNGIGE FAHRZEUGE (OHV)
- Fälle
- Radnaben
- Differential-Gehäuse
BOHRAUSRÜSTUNG
- Gehäuse für Profilköpfe
- Gehäuse von Hydraulikpumpen
Weitere Informationen über den SIFCO Process® erhalten Sie unter info@sifcoasc.com oder telefonisch unter 800-765-4131.
CRAIC ist bereit zum Abflug
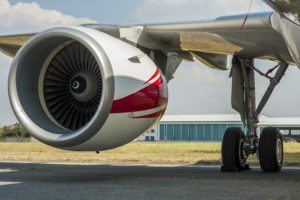
Im vergangenen Monat haben China und Russland gemeinsam die China-Russia Commercial Aircraft International Corporation (CRAIC) gegründet. Ihr Ziel, ein Großraumflugzeug mit zwei Gängen für 280 Passagiere zu bauen, das mit Airbus und Boeing konkurrieren kann, wird schätzungsweise 13 bis 20 Milliarden Dollar kosten. Laut Aviation Week will CRAIC seinen ersten Flug 2022 oder 2023 durchführen und zwischen 2025 und 2027 voll einsatzfähig sein.
Während sich der Hauptsitz und die Montage von CRAIC in Shanghai befinden, wird die Forschung und Entwicklung des Jets in Moskau, Russland, stattfinden. Die Gruppe, die noch in den Kinderschuhen steckt, sucht nun nach Motorenlieferanten. Wie die anderen modernen Jets wird auch das chinesisch-russische 280-Sitzer-Flugzeug oder C929 (sein unbestätigter Name) höchstwahrscheinlich in die globale Lieferkette integriert und Triebwerkshersteller wie Pratt & Whitney, GE und Rolls-Royce sowie andere westliche Hersteller wie Honeywell und United Technologies für seine Cockpit-Avionik und Flugsysteme nutzen.
Dies ist eine gute Nachricht für die Oberflächenveredelungsindustrie und möglicherweise auch für die Umwelt. Bei der Entwicklung eines neuen Flugzeugs ist CRAIC nicht verpflichtet, alte Systeme und Zeichnungen zu verwenden, die Kadmiumbeschichtungen als Korrosionsschutz verwenden. Stattdessen können neue, umweltfreundliche und qualitativ hochwertige Alternativen wie Zink-Nickel oder Zinn-Zink verwendet werden. Durch die Aufnahme der neuen Werkstoffe in die Spezifikationen der Erstausrüster können diese auch für Ausbesserungsarbeiten an Fahrwerken, Landeklappen, Buchsenbohrungen und anderen Strukturbauteilen verwendet werden, was im Wesentlichen zur Abschaffung von Cadmium beiträgt.
Der CRAIC ist der Ansicht, dass ein großer Vorteil der Aufhebung des Duopols von Airbus und Boeing in den geringeren Kosten liegt. Sie hoffen, dass durch die Entwicklung eines Flugzeugs mit niedrigeren Betriebskosten mehr internationale Käufer auf den Plan gerufen werden. Sie planen auch den Verkauf von Wartungsdiensten, Logistikdiensten und Upgrade-Paketen, um zusätzliche Einnahmen zu erzielen.
Informationen über Alternativen zu Cadmium finden Sie in unserem Cadmium Knowledge Hub.
Den vollständigen Artikel von Jeffrey Lin und P.W. Singer für Popular Science können Sie unter www.popsci.com lesen.
Bauteilreparatur für die härtesten Maschinen der Welt
Die Verbesserung der Lebensdauer wichtiger Komponenten ist ein wichtiger Faktor für jeden Hersteller, insbesondere für diejenigen, die einsatzkritische Fahrzeuge für hochkorrosive Umgebungen wie den Bergbau entwickeln und produzieren.
In einem schweren Bergbaubetrieb führen die Produktion rund um die Uhr, die unnachgiebigen Betriebsbedingungen sowie die Größe und das Gewicht der Ausrüstung zu Schäden und erheblichem Verschleiß an den üblichen Komponenten. Einige Komponenten sind aufgrund ihrer Größe und ihres Standorts wartungsintensiv, wie z. B. die Hydraulik- und Getriebesysteme sowie die Komponenten des Achsantriebs.
Die Hersteller sind zwar bestrebt, eine Lösung zu finden, um zu vermeiden, dass Teile verschrottet werden müssen, aber sie wollen auch die Leistung der Komponenten maximieren, Ausfallzeiten reduzieren und eine bewährte Reparatur vor dem Ausfall durchführen.
Zu den Vorteilen des selektiven Bürstengalvanisierens gehört die Möglichkeit, die Beschichtung genau auf bestimmte Bereiche eines Bauteils zu fokussieren, so dass die Teile vor Ort beschichtet werden können, was die Ausfallzeiten drastisch reduzieren und Produktionsverzögerungen minimieren kann. Selektive Beschichtungen eignen sich am besten für lokalisierte Bereiche auf Innen- und Außendurchmessern oder flachen Oberflächen. Im Gegensatz zur Tankbeschichtung sind bei der selektiven Bürstenbeschichtung keine aufwändigen Maskierungen oder speziellen Vorrichtungen zur Beschichtung des Bauteils erforderlich.
Wie lange ein Beschichtungsvorgang dauert, hängt in erster Linie von der Menge des aufzubringenden Materials ab. In marktführenden selektiven Bürstenbeschichtungssystemen können Abscheidungenen mit einer 30- bis 60-fachen Geschwindigkeit im Vergleich zur herkömmlichen Tankbeschichtung abgeschieden werden. Die Leistungs- und Kostenunterschiede, die diese Faktoren bei der Wartung, Verbesserung oder Reparatur kritischer Komponenten bewirken können, können erheblich sein.
Schäden durch Verschleiß, Korrosion oder Fehlbearbeitung können zwar durch selektive Bürstenbeschichtung repariert werden, doch sollte diese innovative Lösung nicht nur für Reparaturen oder die Wiederverwendung in Betracht gezogen werden. Die gesamte Palette der verfügbaren Reinmetall- und Legierungsablagerungen bietet eine verbesserte Verschleißfestigkeit, eine höhere Oberflächenhärte, einen geringeren elektrischen Kontaktwiderstand oder Korrosionsschutz; alles wichtige Aspekte für die Bergbauindustrie.
Weitere Informationen über die innovative Technologie und die Lösungen von SIFCO ASC für die selektive Bürstenbeschichtung finden Sie hier: www.sifcoasc.com/mining.
Feiern Sie Direct Lift am Welt-Hubschrauber-Tag
Der Welt-Hubschrauber-Tag ist Sonntag, der 19. August 2018.
Der Welt-Hubschraubertag soll das Bewusstsein für den gesellschaftlichen Beitrag von Hubschraubern schärfen. Wenn wir diese erstaunlichen Maschinen auszeichnen, würdigen wir auch die Industrie, die sie von der Konstruktion über die Piloten bis hin zum Support unterstützt.
Wenn man an Hubschrauber denkt, kommen einem vielleicht Rettungseinsätze, medizinische Transporte, Katastrophenhilfe und Medienberichte in den Sinn. Ihre Verwendung geht jedoch weit darüber hinaus. Weltweit gibt es schätzungsweise über 55.000 Hubschrauber, von denen fast 40 % im Besitz des Militärs sind. Hubschrauber sind wegen ihrer Start- und Landefläche und ihrer Fähigkeit, schwer zugängliche Bereiche zu erreichen, die weder mit einem Fahrzeug noch mit einem Flugzeug erreichbar sind, sehr begehrt.
SIFCO ASC unterstützt die Hubschrauberindustrie seit Mitte der 1970er Jahre. Seit über 40 Jahren verlassen sich führende Hersteller auf das SIFCO-Verfahren® für die selektive Beschichtung von Bauteilen wie Heck- und Hubrotoren, Rohrbaugruppen, Achsen, Bohrungen und mehr.
Bewährte Ergebnisse
Der Heckträger eines Sikorsky SH-60B Seahawk-Hubschraubers weist einen erheblichen Verschleiß an den Stütznasen auf. Aufgrund der Funktion des Pylons – er schwenkt und rastet zur Aufbewahrung ein oder wird zur AOG-Wartung entfernt – müssen die Stütznasen beim Entfernen der Sicherungsstifte nachgearbeitet werden. Durch den Einsatz des SIFCO Process® wird der Beschichtungsvorgang an Ort und Stelle durchgeführt und dauert nur 5 Minuten pro Öse – das spart Stunden an Ausfallzeit.
Bei Lord Corp. führte die Eloxierung des Tanks zu einem Dimensionsverlust am Innendurchmesser des vorderen Scharniers der Rotorbaugruppe des Bell 407-Hubschraubers. Durch die Bearbeitung der Bohrungen wurde zwar das Maß wiederhergestellt, aber auch die Eloxalschicht entfernt. Die selektive Eloxierung wurde aus Gründen des Korrosionsschutzes und der kürzeren Vorlaufzeiten gewählt. An einem Tag wurden 24 Teile fertiggestellt – im Vergleich zu fast vier Tagen bei der Bearbeitung mit Tankeloxal.
Um mehr darüber zu erfahren, wie SIFCO ASC die Luft- und Raumfahrtindustrie unterstützt, besuchen Sie unsere Luft- und Raumfahrt-Webseite. Wenn Sie mehr über den Flug des ersten Hubschraubers der Welt erfahren möchten, lesen Sie unseren Blog: “Diese Woche in der Geschichte – Amerikas erster praktischer Hubschrauber”.
“Das Team von SIFCO ASC hat unsere spezifischen Anforderungen für verschiedene Wartungs- und Reparaturprojekte in der Luft- und Raumfahrt stets verstanden. Der Kundenservice des Teams ist vorbildlich, mit guten Reaktionszeiten bei Anfragen und flexiblen Durchlaufzeiten bei Reparaturen. SIFCO ASC ist ein zuverlässiger Partner von Heliwork Services und bietet die Qualität und den Service, den wir benötigen.”
Cadmium und die Notwendigkeit von Alternativen in der Luftfahrt
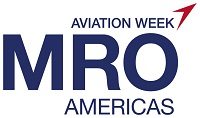
Beim Auspacken nach der MRO Americas haben wir Zeit, unsere Flyer, Visitenkarten und Kleinigkeiten durchzusehen und die gesammelten Informationen und Kontakte zu reflektieren. Hier bei SIFCO war das durchschlagende Thema, das unserem Team auffiel, der Ersatz von Cadmium und der Bedarf an umweltfreundlichen Wartungsalternativen in der Luft- und Raumfahrtindustrie.
Es ist bekannt, dass die anspruchsvolle Luft- und Raumfahrtindustrie ausgereifte Lösungen benötigt, aber viele fürchten sich davor, von den bereits etablierten Anwendungen abzuweichen – obwohl sie ein Risiko für den Betreiber und die Umwelt darstellen können. Und selbst wenn es bewährte Lösungen gibt.
Wir wissen, dass selektive Beschichtungen und Oberflächenveredelungen wesentliche Wartungsanwendungen in der MRO-Branche sind. Aus diesem Grund hat SIFCO seine Produkte in den letzten fünfzig Jahren entwickelt und verfeinert, um qualitativ hochwertige, haftende Abscheidungenen zu liefern, die den sich ständig ändernden Anforderungen der Industrie gerecht werden.
Kadmium ist eine bekannte und weit verbreitete Beschichtung für den Korrosionsschutz von Fahrwerken, Buchsen, Landeklappen und anderen Strukturbauteilen von Flugzeugen. Aber Cadmium ist auch ein bekanntes Karzinogen. Das Risiko, das es für den Betreiber und die Umwelt darstellt, ist der Grund, warum SIFCO vor über 15 Jahren seine Cadmium-Alternativen entwickelt hat.
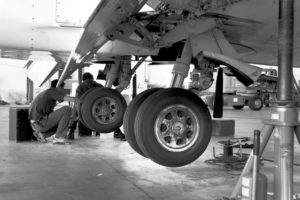
SIFCOs Kadmium-Alternativen sind qualitativ hochwertige Abscheidungenen, die im Kadmium-Beschichtungsprozess als Ersatz verwendet werden können. Zink-Nickel LHE und Zinn-Zink LHE sind weniger toxische Alternativen zu Cadmium, die zur Reparatur von beschädigtem Cadmium, Zink-Nickel, Zinn-Zink und beschädigtem IVD-Aluminium auf hochfesten Stählen verwendet werden können. Beide Beschichtungen bieten einen ausgezeichneten Korrosionsschutz, sind wenig wasserstoffversprödend und erfordern kein nachträgliches Ausglühen zur Beseitigung der Wasserstoffversprödung. In Verbindung mit der dreiwertigen Chromumwandlung von SIFCO können Sie 1.000 Stunden Salzsprühnebel ohne Grundmetallkorrosion erreichen. Diese Zink-Nickel- und Zinn-Zink-Abscheidungenen sind in der Lage, die Leistungsanforderungen von AMS 2451/9, AMS 2451/10 und BAC 5664 zu erfüllen.
Wenn Sie mehr über die Cadmium-Alternativen von SIFCO erfahren möchten, klicken Sie hier oder kontaktieren Sie uns unter info@sifcoasc.com.