Réparation du zinc-nickel endommagé par le placage au pinceau
L’article suivant, rédigé par le responsable technique de SIFCO ASC, Derek Vanek, a été récemment publié dans
Le placage sélectif (au pinceau) est un procédé approuvé de faible fragilisation par l’hydrogène (LHE) utilisé pour appliquer du zinc-nickel sur des zones localisées de composants en acier à haute résistance afin de les protéger contre la corrosion.
Il est utilisé pour appliquer des dépôts localisés sur des pièces précédemment non plaquées ainsi que pour réparer l’usure et la corrosion sur du zinc-nickel précédemment plaqué. Il est approuvé pour la réparation de cadmium et d’aluminium IVD défectueux sur des zones localisées, et existe depuis plus de 20 ans.
Le zinc-nickel est une alternative au cadmium, respectueuse de l’environnement et des opérateurs. Il associe les propriétés de revêtement sacrificiel du zinc à la solidité, la ductilité et la résistance à la corrosion du nickel, créant ainsi une finition de surface qui, dans certains cas, est supérieure à celle du cadmium.
Sa véritable composition d’alliage se situe entre 9 et 14% de nickel, le reste étant du zinc. Grâce à la volonté de l’industrie aérospatiale d’utiliser des alternatives plus sûres et plus respectueuses de l’environnement que le placage au cadmium, les dépôts de zinc-nickel LHE ont connu une utilisation importante au cours des dernières années.
Approuvé par les fabricants du monde entier
Le procédé de placage sélectif de zinc-nickel est approuvé par des fabricants tels que Boeing, Goodrich, Messier-Bugatti-Dowty, Bell, la NASA et Airbus.
Le placage sélectif est une méthode de galvanoplastie bien conçue qui permet de contrôler l’épaisseur des dépôts sur des matériaux de base couramment utilisés pour les composants industriels. Comme son nom l’indique, le processus se concentre sur une zone spécifique, “sélectionnée”, d’un composant.
Le procédé de placage zinc-nickel
La zone à plaquer ainsi que les zones adjacentes qui sont masquées sont nettoyées avec un solvant. Les zones environnantes sont masquées pour les protéger du processus chimique, et cela permet d’isoler la zone qui doit être plaquée. Les matériaux de masquage typiques comprennent les rubans en aluminium et en vinyle, les peintures de masquage et les dispositifs spéciaux. Dans le cas du zinc-nickel, le processus est concentré sur la zone à plaquer. Le masquage est réduit au minimum pour contrôler l’écoulement de la solution sur la pièce.
Le procédé de placage sélectif est hautement portable et peut être utilisé dans l’atelier ou dans le hangar pour travailler directement, in-situ, sur l’avion.
Un équipement minimal est nécessaire pour le processus de zingage-nickel. L’équipement se compose généralement de :
- un redresseur,
- des pistes,
- un outil de métallisation à main (anode),
- et quelques accessoires.
Le volume réel de solution de placage nécessaire sur le chantier pour une réparation typique est inférieur à 1 litre. L’EPI (équipement de protection individuelle) standard comprend des gants, des lunettes de sécurité et une ventilation locale. L’équipement ci-dessous est représentatif de ce qui est nécessaire pour le placage sélectif.
Zinc-nickel LHE – répondre aux spécifications exactes
En plus des nombreuses spécifications commerciales rédigées, l’AMS 2451/9, Brush Plating Zinc-Nickel, Low Hydrogen Embrittlement, a été rédigée spécifiquement pour l’électroplacage sélectif du zinc-nickel.
Le dépôt de type 2 plaqué au pinceau (à l’aide d’un revêtement de conversion au chrome trivalent), testé conformément à la norme ASTM B 117, résistera à 1 000 heures d’exposition à la corrosion par brouillard salin sans aucun signe de corrosion du métal de base ; il passera également les tests de fragilisation par l’hydrogène, les échantillons de traction entaillés étant soumis à un test de charge soutenue de 200 heures à 75 % de la résistance à la traction ultime entaillée. Il est conforme à la norme ASTM F519 et à toutes les exigences fédérales, militaires, AMS et ASTM applicables.
Le placage sélectif du zinc-nickel comme application de réparation des LHE est un processus sûr, simple et beaucoup plus largement utilisé aujourd’hui que ce n’était le cas depuis son développement il y a plus de 20 ans. La certification pour l’utilisation de ce processus est disponible auprès de fournisseurs agréés. Les cours de formation durent généralement trois jours. La recertification des opérateurs est généralement requise chaque année.
Pour en savoir plus sur SIFCO ASC et sur nos services de brossage au zinc-nickel, veuillez nous contacter ici.
Lumières, caméra, action : Le processus SIFCO
Qu’est-ce que le placage sélectif ? Comment fonctionne le Processus SIFCO® ? Quel type de dépôt puis-je effectuer ? Quels sont les avantages du placage sélectif ? Obtenez les réponses à toutes vos questions et plus encore, en regardant notre nouvelle vidéo.
Vous voulez en savoir plus ? Contactez nous à info@sifcoasc.com ou au 800-765-4131.
Amélioration des capacités de traitement grâce à l’automatisation du placage sélectif
La semaine dernière, à l’occasion de l’exposition SUR/FIN de la NASF, Derek Kilgore, ingénieur de projet et de conception mécanique chez SIFCO ASC, a présenté un exposé sur la manière d’améliorer les capacités du processus par l’automatisation du placage sélectif.
Le placage sélectif est une méthode avancée de galvanisation de zones localisées sans utiliser de cuves d’immersion. Plus de trente métaux et alliages purs peuvent être électrodéposés et l’anodisation de type I, II, III, phosphorique et borico-sulfurique peut être appliquée avec précision. Ce processus peut réduire les coûts, les temps d’arrêt et aider les endroits où l’accessibilité est limitée.
Pendant le processus de placage sélectif, les opérateurs peuvent effectuer les tâches suivantes :
- Manipulation des pièces
- Effectuer des inspections visuelles après le placage
- Modifier les paramètres du redresseur (ampères, volts)
- Changer et déplacer les anodes
- Ouvrir et fermer les vannes
- Rincer les pièces
- Déplacer et vider les plateaux de produits chimiques
- Surveiller et documenter les paramètres du redresseur (ampères, volts et ampères-heures)
- Ajuster les ampères-heures en fonction de la durée de vie de la solution
- Maintenir la gravité spécifique de la chimie
- Détecter les problèmes d’équipement
- Gérer les distractions
En raison du nombre de tâches dont un technicien est responsable au cours d’un travail, des variations peuvent se produire dans le placage d’une pièce à l’autre, et d’un opérateur à l’autre.
Afin de réduire le nombre de tâches effectuées, le technicien peut programmer le redresseur pour modifier ses réglages, surveiller le fonctionnement et documenter le réglage. En apportant cette seule amélioration, non seulement l’opérateur n’a plus besoin de modifier et de surveiller le redresseur, mais il peut également apporter les améliorations suivantes au processus :
- Garantit des opérations répétables et reproductibles
- Optimise les propriétés de dépôt avec des ampères, volts et amp ; amp-h
- Augmente le débit
- Permet moins d’erreurs
- Capture l’ampérage, la tension et le temps réels grâce à l’enregistrement des données
- Améliore le contrôle et l’assurance qualité
Mais en poussant les améliorations plus loin et en automatisant l’opération, le technicien n’est plus responsable que de 4 tâches, ce qui élimine complètement l’opérateur et la variation du placage.
- Manipulation des pièces (Charger et décharger des pièces
- Inspection visuelle après placage
- Ajuster les ampères-heures en fonction de la durée de vie de la solution
- Maintenir la gravité spécifique de la chimie
Avec un système automatisé, la variation d’un opérateur à l’autre est éliminée et le placement, le mouvement et la pression de la pièce sont les mêmes pour chaque pièce. Non seulement il offre les avantages d’un redresseur programmé, mais il optimise également les propriétés du dépôt avec des ampères, des volts et des ampères-heures normalisés, un débit accru et une amélioration du contrôle et de l’assurance de la qualité globale. Et en éloignant le technicien de l’opération, les distractions ne sont plus un souci, pas plus que les risques ergonomiques qu’il encourt.
Les données recueillies ont confirmé les affirmations selon lesquelles des améliorations positives ont été apportées lors de l’introduction de l’automatisation. Pour l’échantillon, 2 types de pièces ont été plaquées, de configuration similaire, et une analyse de l’épaisseur a été mesurée sur la pièce 1 dans 4 zones prédéterminées. L’épaisseur a été vérifiée au début du cycle de placage et environ toutes les 12 pièces. Cela a représenté environ 25 échantillons de 450 pièces plaquées sur une période d’un mois. Et pour les pièces plaquées manuellement, 3 techniciens différents ont été utilisés.
Dans les données du redresseur manuel ou contrôlé par l’opérateur, un Sigma de 1,5 ou un Cpk de 0,5 a été enregistré.
Dans l’ensemble, en automatisant le processus à l’aide d’un contrôleur logique programmable, les techniciens peuvent examiner les données capturées par l’interface homme-machine pour déterminer si l’opération a été réalisée dans les limites de la tolérance et améliorer efficacement les valeurs Cpk. En cas d’erreur ou de non-respect des normes de qualité, les techniciens peuvent examiner les données, remonter à la source de l’erreur et prendre les mesures correctives appropriées, afin d’éviter que les erreurs ne se reproduisent.
Comment l’IPS contribue au succès américain

Integrated Power Services (IPS) est le premier fournisseur indépendant de services de réparation et de maintenance de moteurs électriques, de générateurs et de composants mécaniques de transmission de puissance aux États-Unis. Couvrant l’ensemble de l’Amérique du Nord 24 heures sur 24 et 7 jours sur 7, IPS intègre et fournit des services de réparation, des services sur le terrain et des ventes de produits à des milliers de clients travaillant dans des industries à forte intensité d’actifs. Et depuis plus de trente ans, IPS utilise le procédé SIFCO® de placage sélectif pour réparer et protéger des composants critiques tels que les ajustements de roulements sur les arbres, les tourillons d’arbres et les alésages de cloches d’extrémité.
L’approche de SIFCO ASC a démontré, au fil des décennies, qu’elle permettait d’obtenir des résultats constants dans la métallisation d’une large gamme de matériaux et de composants. Contrairement au soudage, qui peut déformer les matériaux environnants et générer un surcroît de travail lors de l’usinage, le SIFCO Process® laisse la zone environnante largement intacte et – pour autant que la surface soit correctement préparée pour l’application – l’adhérence est superbe.
Chez IPS, l’approche SIFCO ASC est utilisée pour plaquer du nickel sur une épaisseur allant jusqu’à 0,030″ au total, ou 0,015″ de chaque côté d’un tourillon ou d’un boîtier. Bien qu’il soit possible de construire des couches plus épaisses, cela implique d’arrêter et de redémarrer le processus et les opérateurs IPS préfèrent ne pas le faire. L’entreprise utilise le procédé de placage SIFCO principalement pour les composants de petite et moyenne taille, mais aussi pour certaines réparations de gros composants de moteurs.
Pour IPS, la solution de placage identifiée il y a plus de 30 ans est toujours aussi utile aujourd’hui – et qu’elle continue à l’être. Matt Peterson, superviseur de l’atelier d’usinage d’IPS, conclut : “SIFCO ASC a fait partie intégrante de la croissance de notre division de service de réparation au cours des trois dernières décennies. Ils ont élargi notre capacité de réparation grâce à leurs produits et processus, formé nombre de nos opérateurs pour améliorer leurs compétences et offert des conseils techniques continus dans des situations de réparation uniques et lorsque le dépannage d’un problème était nécessaire. Je les recommande vivement.”
Lisez l’article complet dans Products Finishing sur PFonline.com.
Aidez à protéger vos cours d’eau locaux
Il y a 45 ans, le 15 avril 1972, les États-Unis et le Canada ont signé l’Accord relatif à la qualité de l’eau dans les Grands Lacs.
Il a été reconnu, en 2012, que l’accord devait être actualisé et renforcé afin d’atteindre ses buts et objectifs. Et en janvier 2017, la première évaluation triennale des progrès réalisés en matière de qualité de l’eau des Grands Lacs a été publiée dans le but de servir de ” catalyseur à l’engagement public. ” La Commission mixte internationale (CMI) cherche à obtenir des réponses et des avis de personnes qui “apprécient les Grands Lacs et souhaitent qu’ils soient utilisés et protégés de manière durable”.
Maintenant, la CMI veut que vous partagiez vos opinions sur les progrès réalisés par les deux gouvernements. Les citoyens des deux pays peuvent participer à une série de discussions et de réunions en ligne et en personne jusqu’au 15 avril 2017. Vos idées contribueront à la première évaluation par la CMI des progrès réalisés par les gouvernements pour restaurer et protéger les Grands Lacs en vertu de l’Accord révisé de 2012.
SIFCO ASC, pourquoi partagez-vous cette information ?
Les Grands Lacs constituent le plus grand réseau d’eau douce de la planète. Selon la Chambre de commerce maritime, la Voie maritime des Grands Lacs fournit 277 000 emplois, produit 35 milliards de dollars de revenus commerciaux et “soutient la santé économique du cœur industriel de l’Amérique du Nord et du marché de consommation de plus de 100 millions de personnes”. La protection et le maintien de la santé des lacs sont aussi simples que la mise en œuvre de pratiques d’élimination sûres.
Lorsque les solutions de placage SIFCO Process ont été utilisées au maximum de leur potentiel, elles sont considérées comme des déchets dangereux et doivent être éliminées conformément aux réglementations de l’EPA. Vous ne devez jamais éliminer une solution de placage par les égouts locaux.
Les solutions épuisées et les eaux de rinçage peuvent être mélangées dans un récipient approprié pour les déchets dangereux. Ces déchets liquides peuvent être accumulés dans un fût en polyéthylène moulé (UNIHI).
En revanche, les déchets solides (tels que les anodes, les couvertures, les rubans et les lingettes) peuvent être stockés dans un fût en plastique à tête ouverte (UN1H2).
SIFCO recommande vivement de tenir un registre des déchets pour enregistrer la quantité et le type de déchets introduits dans le fût afin de faciliter le profilage des déchets lors de l’expédition des fûts vers une installation de traitement, de stockage et d’élimination agréée.
Pour une assistance technique sur les questions d’environnement et de déchets, contactez notre département de sécurité.
SIFCO Concepts de surface appliqués
5708 Schaaf Road
Cleveland, Ohio 44131-1394
TÉLÉPHONE : (216) 524-0099
FAX : (216) 524-6331
Site de production européen
Unité 12-14
Aston Fields Trading Estate
Bromsgrove, Worcestershire
(B60 3EX) Angleterre
TÉLÉPHONE : 011 44 1527-557740
FAX : 011 44 1527-832856
Le maintien de la santé de nos masses d’eau et de nos cours d’eau n’est pas seulement la responsabilité de nos gouvernements, mais aussi de ceux qui vivent à proximité et autour d’eux.
Éoliennes flottantes – l’avenir des énergies renouvelables
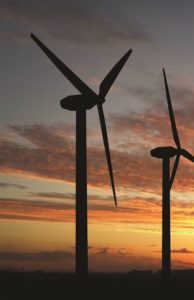
Alors que d’ici la fin de la décennie, 38 000 mégawatts d’éoliennes devraient être fixés au fond de la mer, le comté d’Aberdeen, en Écosse, pourrait en récolter les fruits d’ici la fin de l’année. S’affirmant comme la nation leader dans “l’innovation et le déploiement de l’éolien offshore flottant”, l’Écosse a déjà accordé des permis de construire pour une capacité de 92 mégawatts de la part de plusieurs développeurs d’énergie renouvelable.
Si la société norvégienne Statoil a été la première à recevoir une autorisation en mai 2016, la plus grande ferme est celle de la société écossaise Kincardine Offshore Windfarm Ltd, qui a reçu l’autorisation en mars 2017. Kincardine érigera huit turbines de six mégawatts à environ 15 km des côtes d’Aberdeen et pourra alimenter 56 000 foyers.
D’autres projets de parcs éoliens flottants sont en cours :
- L’entreprise irlandaise Gaelectric Holdings Plc. et la société française Ideol SAS approuvée pour les eaux irlandaises.
- La société suédoise Hexicon AB au large d’Inverness.
- La société japonaise Toda Corp. au large des côtes de Nagasaki.
Cette technologie naissante a été inspirée par l’industrie pétrolière offshore, dont les plates-formes résistent depuis des décennies aux vents violents et aux profondeurs de l’océan. Les turbines flottantes seront moins coûteuses et nécessiteront moins de matériaux que les turbines offshore traditionnelles, qui sont enfoncées dans le fond de la mer à des profondeurs de 40 mètres ou plus. Flottant sur un tube d’acier contenant un ballast, la base de chaque turbine sera ensuite attachée au fond de la mer pour la soutenir.
La côte écossaise est soumise à certains des vents les plus forts, ce qui en fait un endroit idéal pour les parcs éoliens. Mais les vents violents et l’eau de mer se combinent pour créer un environnement extrêmement corrosif. Les finitions de surface des revêtements sacrificiels et des matériaux résistant à l’usure pour les arbres de turbine peuvent prolonger la durée de vie des équipements et réduire les taux de rebut. Grâce aux résultats prouvés par l’industrie pétrolière et gazière offshore, l’utilisation du procédé SIFCO pour l’électrodéposition sur place des arbres d’entraînement et des paliers permet de réaliser les réparations en une seule équipe, ce qui permet de maintenir les turbines opérationnelles plus longtemps.
La réussite de ces projets est cruciale, car les îles disposant de moins de ressources et de masse terrestre pourraient compter sur les parcs éoliens en mer pour répondre à leurs besoins énergétiques. L’Écosse et les développeurs comptent sur l’expertise acquise en travaillant dans l’industrie pétrolière et gazière offshore et dans d’autres environnements marins pour créer une énergie propre afin d’atteindre leur objectif de produire la moitié de l’énergie à partir de sources renouvelables d’ici 2030.
Alors que le marché du pétrole est en déclin et que les terres et les ressources disponibles continuent de diminuer, l’énergie éolienne offshore répond à ce besoin en tant que solution énergétique prometteuse.
Pour plus d’informations sur le procédé SIFCO et les réparations par placage sélectif, contactez info@sifcoasc.com ou le 800-765-4131.
Prolonger la durée de vie : comment votre équipement pétrolier et gazier peut bénéficier d’un traitement par brossage
Dans l’industrie pétrolière et gazière, les équipements fonctionnent dans des environnements difficiles. Les composants doivent résister à l’usure, à la corrosion, aux fluctuations de température et de pression, et les opérateurs ont besoin de solutions de réparation qui peuvent être réalisées en un minimum de temps – produisant des résultats exceptionnels qui peuvent maintenir les composants protégés contre d’autres dommages.
SIFCO ASC a mis au point un procédé qui permet de réparer des composants de grande taille tels que les composants d’assemblage de BOP, les corps de suspension de tubing, les mandrins intérieurs, les cylindres, les boîtiers, les joints de riser, etc. Certains sans qu’il soit nécessaire de les démonter.
Le procédé SIFCO® de placage sélectif est unique. Il s’agit d’une méthode portable de galvanisation de zones localisées sans utiliser de cuve d’immersion. Le dépôt est appliqué sur les zones usées ou endommagées pour redimensionner, réparer ou améliorer les performances du composant. Les dépôts extrêmement adhérents sont appliqués de manière uniforme et précise, éliminant dans certains cas le besoin de post-usinage. De plus, la main-d’œuvre expérimentée et qualifiée de SIFCO ASC possède les certifications nécessaires pour travailler sur les plateformes pétrolières, ce qui permet un déploiement rapide en cas de besoin.
Le SIFCO Process® est très apprécié dans l’industrie pétrolière et gazière et utilisé sur de nombreuses applications OEM et de réparation. Bien que tous les dépôts soient appliqués dans le strict respect de toute spécification ou exigence de qualité, le procédé répond déjà aux spécifications de FMC, GE Oil & Gas, Halliburton, Schlumberger, Tenaris-Hydril, Vallourec et VAM.
SIFCO ASC est équipé pour soutenir l’industrie et réduire la menace de la corrosion tout en relevant les défis clés que sont l’allongement de la durée de vie des équipements, la réduction des temps d’arrêt et la réduction des coûts d’exploitation.
Pour prolonger la durée de vie de vos équipements, ou si vous souhaitez obtenir plus d’informations sur nos services dans le domaine du pétrole et du gaz, visitez notre page Web. Contactez-nous dès aujourd’hui au 800-765-4131 ou à info@sifcoasc.com.
Assurer des conditions de placage appropriées sous le contrôle direct de l’opérateur
Dans les blogs précédents, nous avons abordé certaines conditions de placage au pinceau sur lesquelles l’opérateur a un contrôle direct pour assurer un dépôt de qualité, telles que la vitesse anode-cathode et la température de placage. Au total, l’opérateur a sous son contrôle direct six conditions de brossage. Outre la vitesse et la température, il s’agit de la couverture de l’anode, de la tension, du renouvellement de la solution et de la surface de contact.
Couvercle d’anode
La couverture de l’anode affecte directement la qualité du dépôt. L’utilisation d’un matériau de couverture approprié permet d’obtenir une qualité de dépôt, une adhérence et une cohésion optimales. Grâce à des années de recherche et d’essais, SIFCO ASC fournit des recommandations sur le matériau de couverture approprié pour chaque solution proposée. Pour déterminer le meilleur matériau de couverture pour votre application, consultez la fiche technique de la solution.
Réapprovisionnement de la solution
Le maintien d’une quantité adéquate de solution de placage sur la pièce est également un facteur contrôlable important. Au fur et à mesure que la solution est utilisée, elle s’appauvrit en ions métalliques. Le réapprovisionnement en solution fraîche est essentiel pour maintenir les caractéristiques de dépôt souhaitées. Veillez à pomper la solution assez rapidement ou à tremper assez souvent pour que les ions métalliques dans la zone de travail soient représentatifs du volume total de la solution utilisée.
Zone de contact
Un bon dépôt sera appliqué aussi rapidement que possible lorsque la zone de contact entre l’outil de placage et la pièce est optimale. La zone de contact optimale (OCA) est la meilleure zone de contact possible qui peut être obtenue, compte tenu de la géométrie de la surface à plaquer, de l’ampérage maximal du bloc d’alimentation et de la densité de courant moyenne de la solution de placage utilisée.
La sélection ou la conception adéquate de l’outil de métallisation est la première étape pour obtenir la surface de contact appropriée. L’outil doit toutefois être utilisé correctement, notamment :
Maintenir l’outil sur la zone à plaquer.
Maintenir l’outil en contact ferme et plat avec la zone.
Les outils standard de SIFCO ASC sont disponibles pour préparer et plaquer efficacement une grande variété de tailles et de formes de pièces. Les outils standard peuvent être choisis s’ils répondent aux exigences suivantes :
Outils préparatoires
Couvrir au moins 10 % de la surface à revêtir, si possible.
Couvrir toute la longueur.
Outils de placage
Prévoyez une surface de contact adéquate.
Couvrir toute la longueur.
Prévoyez une solution de pompage si nécessaire.
Tension
La tension est la dernière condition de placage et la plus facile à contrôler ; elle nécessite des modifications rapides et légères à l’aide de la commande de tension. Chaque solution est utilisée dans une certaine plage de tension. La plage de tension assez large est répartie en fonction de la taille de l’outil de galvanisation.
Utilisez la gamme de tension inférieure de 6 à 13 lorsque vous utilisez un petit outillage et que les conditions de placage ne sont pas favorables – par exemple lorsqu’il est difficile d’obtenir une vitesse optimale entre l’anode et la cathode ou lorsqu’il faut plonger pour obtenir la solution plutôt que d’utiliser une pompe. Utilisez la gamme de tension plus élevée de 13 à 20 lorsque vous utilisez des outils plus grands et que les conditions de placage sont favorables.
En contrôlant les six conditions de brossage, l’opérateur peut garantir un dépôt de haute qualité avec une adhérence supérieure. Si vous avez une opération à fort volume, vous pouvez envisager d’automatiser votre opération. Dans notre blog “Improved Process Capabilities Through Automation of Selective Plating”, nous expliquons comment l’automatisation peut tripler les tâches de l’opérateur. Avec un système automatisé, les variations d’un opérateur à l’autre sont éliminées, avec un positionnement, un mouvement et une pression identiques pour chaque pièce.
Si vous avez des questions sur la façon de contrôler l’une des conditions de placage, veuillez contacter notre service technique au 800-765-4131 ou à l’adresse info@sifcoasc.com.
Ingénierie du traîneau du Père Noël
Ce qui suit est un blog invité de Surface Technology
Dans quelques jours à peine, le Père Noël quittera le pôle Nord dans son célèbre traîneau rouge. Chargé des incontournables jouets Hatchimals et Star Wars de cette année, il parcourra 317 millions de kilomètres à travers les océans et les continents pendant toute la nuit du réveillon de Noël.
Alimentés par un mélange de biscuits, de chocolat chaud et de carottes, le Père Noël et ses rennes ont une tâche énorme à accomplir pour s’assurer que les millions d’enfants du monde entier reçoivent leurs cadeaux de Noël.
Nous avons pensé essayer de nous faire une idée de l’ingénierie de surface nécessaire pour que le Père Noël et ses rennes accomplissent leur mission annuelle épique.
Malheureusement, nous ne disposons d’aucune information en provenance du très secret Elf R&D – sans doute le centre de recherche et de développement le plus éminent au monde – mais en faisant appel à notre propre équipe technique, nous avons examiné les exigences uniques du traîneau du Père Noël et avons décrit le mélange de revêtements qui pourrait bien être utilisé.
Le traîneau
Avec seulement une fenêtre de 32 heures pour effectuer toutes ses livraisons, la rapidité est essentielle pour le Père Noël. Il existe de nombreuses théories sur la façon dont le traîneau est propulsé à 0,97 % de la vitesse de la lumière – du renne partageant le même nutritionniste que l’équipe olympique russe de 2012 à la propulsion par fusée.
Ce que nous savons cependant, c’est qu’un revêtement capable de fonctionner efficacement à des températures élevées sera important. Les revêtements céramiques, tels que ceux utilisés par la NASA sur ses navettes spatiales, sont une option viable pour les panneaux de carrosserie du traîneau.
Pulvérisation thermique, telle que HVOF peut également être utilisé pour tous les composants mobiles, tels que les composants des turbines (en cas de propulsion par fusée), en raison de sa capacité à fonctionner à des températures élevées et à offrir une meilleure protection contre l’usure, la corrosion, la fatigue et l’oxydation à haute température – la dernière chose dont le Père Noël a besoin est un dysfonctionnement mécanique avec un calendrier aussi serré.
Coureurs de traîneaux
Avec autant de livraisons à effectuer, les coureurs au pied du traîneau du Père Noël vont effectuer des millions d’atterrissages et de décollages. Un jouet cassé ne fera pas l’affaire le matin de Noël. Un atterrissage en douceur est donc essentiel.
Nous pensons que le placage sélectif est peut-être utilisé chaque année dans l’atelier des lutins pour s’assurer que les patins du Père Noël sont entretenus et prêts pour le décollage de Noël. En utilisant le SIFCO Process®, le nickel ou le cadmium peut être utilisé pour replaquer les zones usées ou ébréchées des patins. De plus, le processus est approuvé par la FAA, ce qui évite au Père Noël de se retrouver sur la liste des vilains de la Federal Aviation Authority.
Freins
Nous supposons que les rennes font partie intégrante de l’arrêt du traîneau à chaque point de chute, mais pour un peu plus de puissance d’arrêt, les lutins du Père Noël ont peut-être opté pour un système de freinage mécanique. Une combinaison de placage en alliage de zinc et de revêtement en poudre (RAL 3020, bien sûr), voire un revêtement en céramique, pourrait être utilisée pour s’assurer que le Père Noël ne manque pas un arrêt.
Contrôle de la climatisation
En parcourant le ciel de l’Afghanistan au Zimbabwe, en passant par 194 pays, le Père Noël sera exposé à des températures allant de moins de zéro à plus de 95 degrés.
Nous présumons que le costume du Père Noël est fabriqué à partir des meilleurs matériaux performants de Laponie, dans un souci de chaleur et de respirabilité, mais pour plus de confort, en particulier dans les climats chauds, les elfes ont peut-être équipé le traîneau du Père Noël de la climatisation.
Alors que Surface Technology, SIFCO ASC et Ultraseal fournissent des services pour de nombreux projets d’ingénierie et de fabrication passionnants, la réponse à la question de savoir comment le Père Noël et ses rennes livrent tous ces cadeaux la veille de Noël devra rester un mystère pour une autre année.
Nous souhaitons à tous nos clients du monde entier un très joyeux Noël et une nouvelle année prospère.
Découvrez l’efficacité des réparations aérospatiales grâce à un webinaire
Chez SIFCO ASC, nous savons que l’atteinte de niveaux d’efficacité plus élevés est peut-être l’un des plus grands défis auxquels sont confrontés nombre de nos clients. Pour l’industrie aérospatiale, qui connaît une forte augmentation de la demande dans le secteur commercial, l’efficacité est encore plus importante. Si l’on ajoute à ce défi les exigences législatives qui régissent l’utilisation de produits chimiques tels que le cadmium, les acteurs du secteur sont confrontés à un paysage opérationnel difficile.
Séminaire en ligne gratuit : Placage à la brosse et anodisation pour l’aérospatiale
C’est pourquoi SIFCO ASC organise un webinaire gratuit. Présenté par Danijela Milosevic-Popovich – responsable de la recherche et du développement de SIFCO ASC – Spec’d In : Brush Plating & Anodizing for Aerospace fournira des informations et des conseils d’experts aux fabricants de l’industrie aérospatiale.
Conçu pour donner un aperçu des moyens de surmonter les défis auxquels sont confrontés les fabricants et les opérateurs aujourd’hui, le webinaire aidera les participants à comprendre les processus de placage sélectif et d’anodisation et la manière dont ils améliorent les options de réparation efficaces pour les composants aérospatiaux.
Les avantages du placage sélectif par rapport au placage en cuve
Danijela a déclaré : “Notre webinaire est conçu pour fournir aux participants un aperçu expert de l’utilisation du placage sélectif et de l’anodisation, et de la façon dont ces processus contribuent à une plus grande efficacité dans la chaîne d’approvisionnement de l’aérospatiale. Ces processus sont déjà spécifiés dans les manuels de révision et de pratiques standard. Ce webinaire examinera donc quand et pourquoi ces processus doivent être utilisés plutôt que des alternatives telles que le placage de réservoir. Nous partagerons également des exemples concrets qui démontrent les économies de temps et de coûts associées aux processus, ainsi que la manière dont les clients peuvent utiliser l’automatisation pour améliorer la qualité et la cohérence de leurs opérations de placage.
Une plus grande efficacité pour l’aérospatiale
“L’industrie aérospatiale traverse actuellement une période à la fois passionnante et difficile. Le secteur est extrêmement dynamique, avec une demande croissante, mais cela met à rude épreuve les fabricants tout au long de la chaîne d’approvisionnement, tandis que le marché MRO subit une pression accrue pour maintenir les avions en service le plus longtemps possible. Notre webinaire aidera les fabricants à comprendre comment ils peuvent maximiser leur efficacité, ce qui les rendra plus compétitifs et élèvera les niveaux de qualité dans l’ensemble du secteur.”