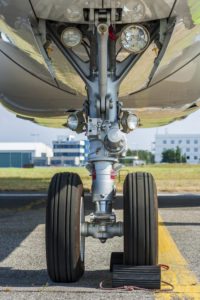
Cadmium plating is often used in aerospace applications as the industry requires well-engineered and proven deposits that minimize the risk to the operator and the environment. But, with it being removed from commercial use, many businesses will need to use alternatives.
What is cadmium plating?
Cadmium plating is a metallic silver coating that provides excellent corrosion resistance and could be deposited on various materials including steel, copper, iron, brass, and aluminum.
In the plating industry, it is used as a sacrificial coating. So, it is ideal for corrosive environments and can protect the underlying base metal, such as steel, even if it’s scratched or corroded. This is why it was often used in the aerospace industry, particularly for landing legs/gears.
Why is cadmium plating banned?
According to the Environmental Protection Agency (EPA), cadmium is highly toxic and exposure to it and its compounds can cause health problems. These include pulmonary irritation, kidney disease, and lung cancer. Cadmium is also an IARC Group 2A material that leeches easily, so it isn’t environmentally friendly.
Under the European REACH statute, cadmium plating is banned except for certain uses. And worldwide cadmium plating has been removed from almost all commercial uses. The only remaining uses are aircraft and military applications, however it’s expected these will be phased out too.
This is why cadmium alternatives, like Zinc-Nickel, are used for many cases instead.
Alternatives to cadmium plating:
For the aerospace industry, Zinc-Nickel LHE and Tin-Zinc are less toxic alternatives to cadmium that can be used to repair damaged cadmium, zinc-nickel, tin-zinc, and damaged IVD aluminum on high strength steels. Both deposits provide excellent corrosion protection and are LHE, and do not require a post-plating, hydrogen embrittlement relief bake.
SIFCO ASC’s cadmium replacements:
At SIFCO ASC, we’ve been developing cadmium replacements since 1992, to meet Boeing’s specifications and demand for an environmentally friendly alternative. Boeing began their research into cadmium alternatives in the early 1970’s as a response to Japan’s ban of the use of cadmium in 1969.
According to Mary J. Nelson and Earl C. Groshart of the Boeing Defense & Space Group: “In 1990, Environmental Protection Agency’s (EPA) “33/50” Plan for reduction of 17 chemicals including cadmium and cyanide became a goal for Boeing to reduce its hazardous chemical usage.”
To date, SIFCO ASC has two cadmium plating alternatives which provide corrosion resistance, lubricity, and low hydrogen embrittlement. Zinc-Nickel LHE, Code 4018 and Tin-Zinc, Code 4019 both meet aerospace spec AMS 2451, while 4018 also meets AMS 2417, and 4019 meets AMS 2434. These superior quality deposits can be applied anywhere, in the shop or in the field.