What is Selective Plating?
Selective electroplating is a portable plating method used to enhance, repair, and refurbish localized areas on manufactured components
The SIFCO Process® is the leading portable method of selective plating localized areas without the use of an immersion tank. It is primarily used for enhancing surfaces on OEM components, permanent repairs and salvaging worn or mis-machined parts.
Selective plating includes processes in which solution can be applied via a brush or encapsulated or cell plating flow tools.
Brush Plating – This is the primary technique used by SIFCO ASC technicians. In this process, a direct current -supplied by a rectifier – is used in a circuit that’s complete when an anode is touching the component to be plated. When brush plating, the anode acts as the brush which is covered in cotton, polyester or other materials that hold solutions. Once the anode is thoroughly saturated in the solution the deposit is applied onto the negatively charged part. Brush plating requires movement between the anode and the part. This can be accomplished by brushing the anode over the part, by moving the part and keeping the anode stationary, or by moving both.

Brush Plating
This is the primary technique used by SIFCO ASC technicians. In this process, a direct current -supplied by a rectifier – is used in a circuit that’s complete when an anode is touching the component to be plated. When brush plating, the anode acts as the brush which is covered in cotton, polyester or other materials that hold solutions. Once the anode is thoroughly saturated in the solution the deposit is applied onto the negatively charged part. Brush plating requires movement between the anode and the part. This can be accomplished by brushing the anode over the part, by moving the part and keeping the anode stationary, or by moving both.
Brush plating is best suited for applications where single or low numbers of components are in need of repair or refurbishment. For applications with high quantities of components, SIFCO ASC provide custom solutions for automating the SIFCO Process®. Tailored solutions range from customized workstations through to fully automated systems
Learn More About Brush Plating >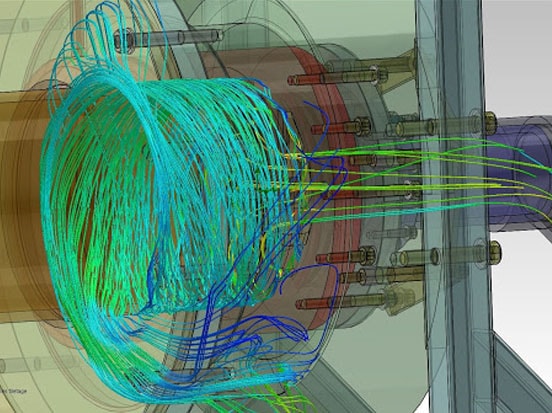
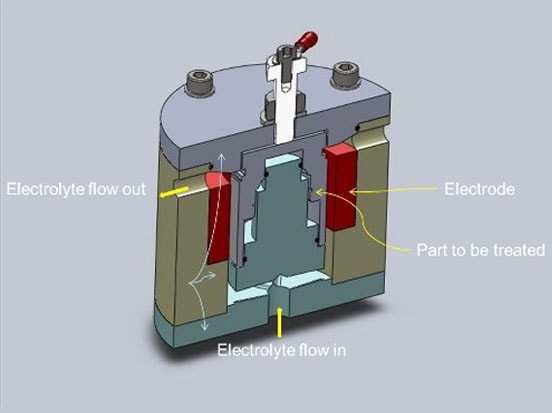
Encapsulating Flow Plating
For applications where the surfaces to be treated are more complex and are not as easily accessible with brush plating, SIFCO ASC has developed a method for selective flow plating. In such cases, custom all-in-one tooling is used to isolate then pass plating solutions over the area.
State-of the-art, customized anodes are designed to match the complex geometry of the selected area. The tooling uses custom-fit seals to encapsulate the area and allows for space between the anode and the component. Electrodeposition occurs when the electric current is passed through the chemistry as it flowed over the area. In many cases, multiple steps – activation, rinse, plating, etc. – can be completed within the same tool and without removal of the part.
Flow plating is a “one piece flow” process. It provides the full history of all critical process parameters for each high value part plated. One piece flow also limits the amount of reworks in the instance of any process deviation.
Flow plating can be applied to small and large scale components alike, and can be equally suitable for low to high quantities. As with brush plating, if volumes are low, the operation can be performed manually, but for higher quantities SIFCO ASC offers fully automated flow plating systems
Learn More About Encapsulating Flow Plating >Dripless Plating
For a wide range of industries – from aerospace to military, marine, petrochemical, oil and gas, and paper – selective electroplating is preferable to conventional thermal spray and tank plating methods.
Why? Its ability to be performed on site simply makes it an inherently environmentally-friendly option. Not to mention that the system is portable – enabling it to be wheeled directly to the specific part or component.
The SIFCO That means all chemical solutions are recycled back into the cart’s solution management system right at the surface of the workpiece without the use of trays to catch the solution – providing a clean and efficient work environment.
Advanced Solution Control System >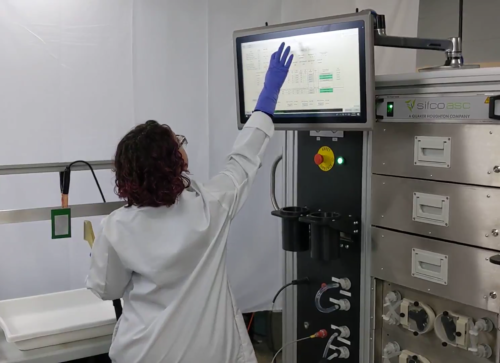